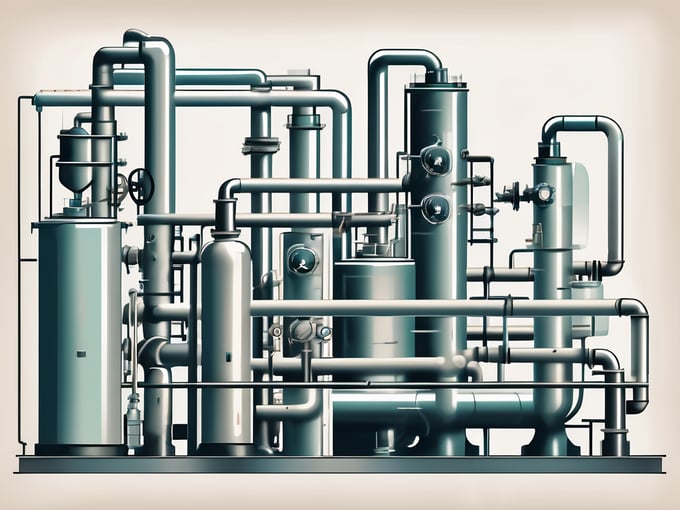
Guide to Preventative Maintenance for Plant Operators in the Groundwater Management Industry
In the groundwater management industry, preventative maintenance plays a crucial role in ensuring the smooth operation of plant facilities. This comprehensive guide will provide plant operators with valuable insights into the importance of preventative maintenance, strategies for implementation, scheduling and planning, safety considerations, training and skills development, as well as evaluating the success of their maintenance program.
Understanding Preventative Maintenance
Groundwater management involves numerous processes and equipment that require regular maintenance to prevent costly breakdowns and ensure optimal performance. Preventative maintenance involves proactively identifying potential issues and addressing them before they lead to unplanned downtime or failures.
The Importance of Preventative Maintenance in Groundwater Management
Preventative maintenance is of utmost importance in groundwater management as it helps extend the lifespan of equipment, reduces repair costs, and minimizes the risk of environmental contamination. By regularly inspecting and maintaining equipment, plant operators can identify and resolve minor issues before they escalate into major problems.
One of the key reasons why preventative maintenance is crucial in groundwater management is its ability to extend the lifespan of equipment. Groundwater management systems often consist of complex machinery, such as pumps, valves, and filters, which are subjected to continuous use and wear. Without regular maintenance, these components can deteriorate over time, leading to decreased efficiency and eventual failure. By implementing a preventative maintenance program, operators can proactively address any signs of wear, leakage, or damage, ensuring that the equipment remains in optimal condition for a longer period.
Another significant benefit of preventative maintenance is its cost-saving potential. Unplanned breakdowns and repairs can be expensive, not only in terms of the repair itself but also due to the potential loss of production and revenue. By regularly inspecting and maintaining equipment, operators can identify and resolve minor issues before they escalate into major failures, saving both time and money. Additionally, preventative maintenance can help optimize the performance of equipment, leading to energy savings and reduced operational costs in the long run.
Furthermore, preventative maintenance plays a crucial role in minimizing the risk of environmental contamination. Groundwater management systems are responsible for maintaining the quality and safety of groundwater resources. Any malfunction or failure in the equipment can result in contamination, which can have severe consequences for both human health and the environment. By implementing a preventative maintenance program that includes regular inspections and maintenance tasks, operators can ensure that the equipment is functioning properly, reducing the likelihood of contamination incidents.
Key Components of Preventative Maintenance
Successful preventative maintenance programs comprise three main components:
- Inspection: Regularly inspecting equipment, including pumps, valves, and filters, allows operators to identify any signs of wear, leakage, or damage. During inspections, operators can also assess the overall condition of the equipment and identify any potential areas of concern. This proactive approach enables timely repairs or replacements, preventing unexpected breakdowns and ensuring continuous operation.
- Preventative Tasks: Performing routine tasks like lubrication, cleaning, and calibration helps ensure equipment operates efficiently and reliably. Lubrication prevents friction and wear, while cleaning removes any debris or contaminants that may hinder performance. Calibration ensures that the equipment is operating within the desired parameters, optimizing its functionality. By regularly performing these preventative tasks, operators can maintain the equipment's performance and prevent potential issues from arising.
- Record Keeping: Keeping detailed records of maintenance activities, repairs, and equipment performance allows for better planning and analysis of trends. These records provide valuable insights into the history of the equipment, including past issues and their resolutions. By analyzing the data, operators can identify recurring problems, evaluate the effectiveness of maintenance strategies, and make informed decisions regarding equipment replacement or upgrades. Additionally, record keeping ensures compliance with regulatory requirements and facilitates communication between maintenance teams and management.
Implementing Preventative Maintenance Strategies
Developing a comprehensive preventative maintenance plan is essential for effective implementation. By implementing preventative maintenance strategies, businesses can minimize equipment downtime, reduce repair costs, and increase overall operational efficiency.
Preventative maintenance involves performing regular inspections, cleaning, and servicing of equipment to prevent potential breakdowns and extend its lifespan. It is a proactive approach that focuses on identifying and addressing issues before they escalate into major problems.
Steps to Develop a Preventative Maintenance Plan
To create a maintenance plan, there are several important steps to follow:
- Identify Equipment: Make a list of all the equipment and systems that require maintenance. This includes machinery, HVAC systems, electrical systems, and any other critical components.
- Establish Maintenance Tasks: Determine the specific tasks needed for each equipment or system. This may include lubrication, filter replacement, calibration, inspection, and testing.
- Create Schedule: Develop a maintenance schedule that outlines when each task should be performed. Consider factors such as equipment usage, manufacturer recommendations, and industry best practices.
- Allocate Resources: Ensure sufficient resources, such as personnel and tools, are available for maintenance activities. This may involve training staff, acquiring specialized tools, or outsourcing certain tasks to qualified contractors.
- Monitor and Adjust: Regularly review and adjust the maintenance plan based on equipment performance and feedback from operators. This allows for continuous improvement and optimization of maintenance strategies.
By following these steps, businesses can establish a well-structured preventative maintenance plan that aligns with their specific needs and goals.
Tools and Technologies for Preventative Maintenance
Modern technology offers innovative solutions to enhance preventative maintenance efforts. Plant operators can leverage various tools and technologies to streamline their maintenance processes:
- Condition Monitoring Systems: These systems continuously monitor equipment performance and provide real-time data for proactive maintenance. By analyzing data such as temperature, vibration, and pressure, operators can detect early warning signs of potential failures and take corrective actions.
- Computerized Maintenance Management Systems (CMMS): CMMS software enables efficient planning, scheduling, and tracking of maintenance activities. It helps organizations streamline work orders, manage inventory, and generate reports to ensure timely and effective maintenance.
- Predictive Analytics: Utilizing data analysis algorithms, predictive analytics can identify patterns and predict equipment failures, enabling early intervention. By analyzing historical data and real-time performance metrics, operators can make data-driven decisions and optimize maintenance strategies.
These tools and technologies not only improve the accuracy and efficiency of preventative maintenance but also enable businesses to transition from reactive to proactive maintenance approaches. By leveraging data and automation, organizations can reduce unplanned downtime, increase equipment reliability, and ultimately improve their bottom line.
Maintenance Scheduling and Planning
Developing an effective maintenance schedule is vital for optimizing plant operations and ensuring equipment reliability. A well-planned and executed maintenance schedule can help prevent unexpected breakdowns, reduce downtime, and increase overall productivity.
Creating an Effective Maintenance Schedule
When creating a maintenance schedule, there are several key factors to consider:
- Prioritize Tasks: Focus on critical equipment and tasks that directly impact plant operations. By identifying and prioritizing the most crucial maintenance activities, you can allocate resources effectively and ensure that essential equipment receives the attention it needs.
- Consider Asset Age: Older equipment may require more frequent inspections and maintenance. As equipment ages, its performance and reliability may decline, necessitating more frequent monitoring and upkeep. By taking asset age into account, you can develop a maintenance schedule that addresses the specific needs of each piece of equipment.
- Seamless Integration: Schedule maintenance activities during periods of low demand to minimize disruption to plant operations. By carefully planning and coordinating maintenance tasks with production schedules, you can minimize the impact on overall productivity. This can involve scheduling maintenance during planned downtime or coordinating with different departments to ensure a smooth workflow.
- Collaboration: Involve plant operators and maintenance personnel in the scheduling process to gather insights and ensure a well-rounded schedule. By including the perspectives and expertise of those directly involved in plant operations, you can create a more comprehensive maintenance schedule that addresses all relevant factors.
Balancing Maintenance Tasks and Plant Operations
Plant operators must strike a balance between maintenance tasks and ongoing operations to ensure smooth and efficient plant functioning. Here are some strategies to achieve this balance:
- Proactive Planning: Implement planned maintenance during scheduled downtime to avoid interference with regular plant activities. By strategically planning maintenance tasks during periods when production is already halted, you can minimize disruptions and maximize efficiency.
- Effective Communication: Collaborate with plant operation teams to coordinate maintenance activities and schedule changes. Clear and open communication between maintenance personnel and plant operators is crucial for minimizing conflicts and ensuring that maintenance tasks are carried out without hindering ongoing operations.
- Training and Skills Development: Equipping maintenance personnel with the necessary knowledge and skills to efficiently perform tasks is essential. By investing in training and skills development programs, you can ensure that your maintenance team is well-prepared to handle various maintenance activities. This includes staying updated on the latest technologies, best practices, and safety protocols.
By following these guidelines and continuously refining your maintenance schedule, you can enhance plant operations, extend equipment lifespan, and improve overall productivity.
Safety Considerations in Preventative Maintenance
Ensuring safety in preventative maintenance is paramount to protect personnel and the environment. By implementing comprehensive safety measures, organizations can minimize accidents and create a secure working environment.
Identifying Potential Safety Hazards
Before commencing maintenance activities, it is essential to identify potential hazards, such as electrical, chemical, or mechanical risks. Conducting a thorough risk assessment allows maintenance teams to understand the potential dangers associated with specific tasks and take appropriate precautions.
For example, when dealing with electrical equipment, it is crucial to be aware of the risk of electric shock. By identifying potential electrical hazards, such as exposed wires or faulty equipment, maintenance personnel can take necessary steps to mitigate the risks, such as wearing insulated gloves and using non-conductive tools.
Similarly, in environments where hazardous chemicals are present, it is vital to identify the potential risks associated with handling and storing these substances. By implementing proper ventilation systems, providing appropriate personal protective equipment (PPE), and ensuring proper labeling and storage of chemicals, organizations can minimize the risk of chemical exposure and related accidents.
Incorporating Safety Measures in Maintenance Plans
Integrating safety measures into maintenance plans is crucial to prevent accidents and protect personnel. By considering safety as an integral part of the maintenance process, organizations can create a culture of safety and ensure that all maintenance activities are carried out with utmost care.
One important safety measure is the use of Personal Protective Equipment (PPE). Ensure all personnel have access to appropriate PPE, such as gloves, goggles, and protective clothing. By providing the necessary protective gear, organizations can minimize the risk of injuries and ensure the well-being of their employees.
Another essential safety measure is the implementation of lockout/tagout procedures. This involves following proper protocols to isolate energy sources and prevent accidental equipment starts. By effectively locking out and tagging out equipment, maintenance personnel can protect themselves from unexpected energy releases and potential injuries.
Training and education are also crucial components of a comprehensive safety plan. Providing regular safety training to personnel raises awareness and knowledge of potential risks. By educating employees on safe work practices, organizations empower their workforce to identify and address safety hazards, reducing the likelihood of accidents.
Furthermore, organizations should establish clear communication channels for reporting safety concerns. Encouraging employees to report any potential hazards or near-miss incidents fosters a proactive safety culture. By promptly addressing reported concerns, organizations can continuously improve their safety protocols and prevent accidents in the future.
In conclusion, safety considerations in preventative maintenance are of utmost importance. By identifying potential safety hazards, incorporating safety measures into maintenance plans, and providing adequate training and education, organizations can create a safe working environment for their personnel. Prioritizing safety not only protects employees but also ensures the smooth operation of equipment and the preservation of the environment.
Training and Skills Development for Maintenance
Effective maintenance requires a skilled workforce equipped with the necessary knowledge and expertise. Without proper training and skills development, maintenance tasks can become challenging and inefficient.
Let's take a closer look at the essential skills that plant operators should possess to ensure smooth and efficient maintenance operations:
Essential Skills for Plant Operators
Plant operators play a crucial role in maintaining the functionality and reliability of equipment and systems. To excel in their roles, they should possess a range of skills, including:
- Technical Knowledge: Understanding the operation and maintenance requirements of various equipment and systems is vital for plant operators. This knowledge enables them to identify potential issues, perform routine maintenance tasks, and troubleshoot problems effectively.
- Troubleshooting Skills: Maintenance tasks often involve identifying and rectifying issues. Plant operators should have the ability to analyze problems, both independently and as part of a team, and implement appropriate solutions promptly. Their troubleshooting skills are crucial in minimizing downtime and ensuring the smooth operation of equipment.
- Communication: Strong communication skills are essential for plant operators to collaborate effectively with their team members and other departments. Clear and concise communication facilitates the exchange of information, enables effective reporting of maintenance activities, and ensures that everyone is on the same page when it comes to maintenance tasks.
Now that we understand the essential skills required for plant operators, let's explore the training programs that can aid in their skills development:
Training Programs for Effective Maintenance
Implementation of training programs can significantly contribute to the skills development of maintenance personnel. These programs provide opportunities for continuous learning and improvement. Here are some effective training approaches:
- Formal Training: Enrolling personnel in courses, workshops, and seminars can enhance their technical knowledge and keep them updated with the latest advancements in maintenance practices. These formal training programs provide structured learning opportunities and cover a wide range of topics, including equipment maintenance, safety protocols, and emerging technologies.
- Mentoring: Pairing experienced maintenance professionals with newcomers can facilitate knowledge transfer and skills development. Mentoring programs allow new employees to learn from seasoned experts, gaining valuable insights and practical tips that are not typically covered in formal training programs. This hands-on guidance helps in building confidence and honing specific maintenance skills.
- On-the-Job Training: Providing hands-on training opportunities is crucial for plant operators to gain practical experience in equipment installations and maintenance tasks. By working alongside experienced technicians, they can learn the intricacies of different equipment, understand common maintenance challenges, and develop problem-solving skills specific to their workplace.
By investing in training and skills development programs, organizations can ensure that their maintenance workforce is equipped with the necessary expertise to handle various maintenance tasks efficiently. Continuous learning not only enhances the capabilities of individual plant operators but also contributes to the overall success and reliability of the maintenance department.
Evaluating the Success of Your Preventative Maintenance Program
Periodically assessing the performance of the preventative maintenance program is crucial.
Key Performance Indicators for Maintenance
Plant operators can utilize various key performance indicators (KPIs) to evaluate the effectiveness of their maintenance program, such as:
- Overall Equipment Efficiency (OEE): Measures the effectiveness of equipment utilization and performance.
- Mean Time Between Failures (MTBF): Calculates the average time between equipment failures.
- Mean Time to Repair (MTTR): Measures the average time taken to repair equipment breakdowns.
Continuous Improvement in Preventative Maintenance
To achieve continuous improvement:
- Feedback and Analysis: Regularly review maintenance records, KPIs, and operator feedback to identify areas of improvement.
- Technological Advancements: Stay informed about emerging technologies and consider their potential in enhancing maintenance practices.
- Collaborative Environment: Encourage a culture of continuous learning and improvement within the maintenance team.
By following the principles of preventative maintenance outlined in this guide, plant operators in the groundwater management industry can significantly enhance the reliability, safety, and efficiency of their operations. Implementing proactive maintenance strategies and investing in skills development will ultimately lead to optimized plant performance and long-term success.