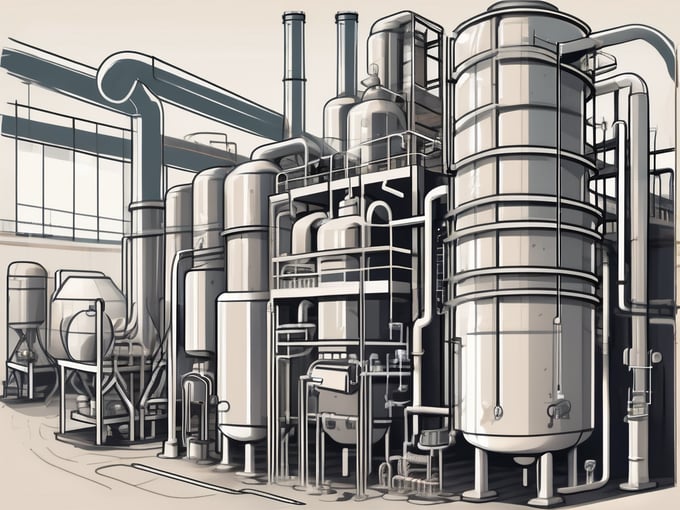
The Ultimate Guide to Preventative Maintenance for Plant Operators in the Sludge Management Industry
Welcome to the Ultimate Guide to Preventative Maintenance for Plant Operators in the Sludge Management Industry!
Understanding Preventative Maintenance
In the sludge management industry, preventative maintenance plays a crucial role in ensuring the smooth operation of plants and equipment. By proactively identifying and addressing potential issues before they escalate, plant operators can minimize downtime, optimize performance, and extend the lifespan of their machinery.
Preventative maintenance involves a systematic approach to maintaining equipment and facilities, focusing on preventing breakdowns and failures rather than reacting to them. It is a proactive strategy that aims to keep everything in working order, reducing the need for costly repairs and replacements.
One of the primary reasons why preventative maintenance is so important in the sludge management industry is the demanding nature of the work. Sludge management plants handle hazardous materials, and any interruption in operations can lead to environmental contamination and health risks. By implementing a comprehensive maintenance program, plant operators can reduce the chances of equipment failure, thereby safeguarding the environment and protecting public health.
The Importance of Preventative Maintenance in Sludge Management
Preventative maintenance is not just about avoiding equipment failures; it also helps in optimizing the overall performance of sludge management plants. Regular inspections and maintenance activities ensure that all components are functioning at their best, maximizing efficiency and minimizing energy consumption.
Moreover, preventative maintenance helps in identifying potential issues that may not be immediately apparent. By conducting routine checks and tests, plant operators can detect early signs of wear and tear, corrosion, or other forms of deterioration. Addressing these issues promptly can prevent them from escalating into major problems that could disrupt operations and incur significant costs.
Another benefit of preventative maintenance in sludge management is the extension of equipment lifespan. By taking care of machinery and ensuring it is properly maintained, plant operators can prolong its useful life. This not only saves money on premature replacements but also reduces the environmental impact associated with manufacturing new equipment.
Key Concepts in Preventative Maintenance
When it comes to preventative maintenance, certain key concepts should guide plant operators. Regular inspections are essential to identify any signs of wear and tear, leaks, or other potential issues. These inspections can be visual, auditory, or even involve the use of advanced technologies such as thermal imaging to detect hidden problems.
Timely repairs are also crucial in preventative maintenance. Once an issue is identified, it should be addressed promptly to prevent further damage or failure. Plant operators should have a well-established system for reporting and addressing maintenance requests, ensuring that repairs are carried out efficiently.
Proper lubrication is another critical aspect of preventative maintenance. Lubricants help reduce friction and wear between moving parts, extending their lifespan. Regular lubrication schedules should be followed, and the correct type and quantity of lubricants should be used to ensure optimal performance.
Calibration checks are necessary for equipment that relies on accurate measurements or settings. Instruments and sensors should be calibrated regularly to ensure their readings are precise and reliable. This is particularly important in sludge management plants, where accurate measurements are crucial for maintaining process efficiency and compliance with regulatory standards.
Lastly, adherence to manufacturer's guidelines is essential in preventative maintenance. Manufacturers provide specific instructions on maintenance activities, including recommended schedules, procedures, and spare parts. Following these guidelines ensures that equipment is maintained correctly and helps preserve warranty coverage.
The Role of Plant Operators in Preventative Maintenance
Plant operators play a pivotal role in implementing and executing preventative maintenance programs. They are responsible for performing daily tasks and adhering to a set of unique skills and knowledge requirements.
Preventative maintenance is a proactive approach to equipment upkeep, aimed at preventing breakdowns and reducing the risk of unplanned downtime. By regularly inspecting, cleaning, and maintaining equipment, plant operators help ensure that the machinery operates at peak performance, minimizing the chances of costly repairs or production interruptions.
One of the key daily tasks of plant operators is conducting visual inspections. By visually examining the equipment, they can identify any signs of wear and tear, leaks, or other potential issues. This allows them to address these problems promptly, preventing them from escalating into major breakdowns.
In addition to visual inspections, plant operators also monitor equipment performance. They keep a close eye on various parameters such as temperature, pressure, and vibration levels. By tracking these metrics, they can detect any abnormal trends or deviations from the norm, which may indicate underlying problems. Identifying these issues early on enables the maintenance team to take corrective action before they lead to equipment failure.
Regular cleaning is another crucial aspect of preventative maintenance. Plant operators ensure that equipment is free from dirt, debris, and other contaminants that can impair its performance. They follow specific cleaning procedures and use appropriate cleaning agents to maintain optimal cleanliness. By keeping the equipment clean, plant operators contribute to its longevity and reliability.
Lubrication is also an essential part of preventative maintenance. Plant operators apply lubricants to moving parts to reduce friction and wear. This helps extend the lifespan of the equipment and ensures smooth operation. They carefully follow manufacturer guidelines to determine the appropriate lubrication schedule and type of lubricant to use for each piece of equipment.
In addition to visual inspections, monitoring, cleaning, and lubrication, plant operators are responsible for conducting calibration checks. Calibration ensures that equipment is accurately measuring and controlling various parameters. By calibrating instruments regularly, plant operators ensure that the readings are reliable and within acceptable limits. This is particularly important for critical processes that require precise control, such as temperature or pressure regulation.
Documenting maintenance activities is an integral part of a successful preventative maintenance system. Plant operators record all maintenance tasks performed, including inspections, cleaning, lubrication, and calibration. These records serve as a valuable resource for tracking equipment history, identifying recurring issues, and planning future maintenance activities. Additionally, plant operators report any anomalies or potential problems to the maintenance team, enabling them to take appropriate action.
Skills and Knowledge Required
Plant operators need a diverse skill set to excel in preventative maintenance. Strong troubleshooting abilities are crucial for quickly identifying and resolving equipment issues. They must be able to analyze symptoms, diagnose problems, and implement effective solutions. This requires a deep understanding of equipment functionality and the ability to interpret technical manuals and diagrams.
Furthermore, plant operators must be familiar with safety protocols to ensure their own well-being and the safety of others. They need to understand the potential hazards associated with operating and maintaining specific equipment and follow proper safety procedures to mitigate risks. This includes wearing appropriate personal protective equipment, using lockout/tagout procedures, and adhering to established safety guidelines.
Plant-specific maintenance practices also play a significant role in the skill set of plant operators. Different industries and plants have unique maintenance requirements and practices. Plant operators must be well-versed in these specific practices to effectively maintain the equipment and systems within their facility. This may include knowledge of specialized tools, techniques, or industry-specific regulations.
In conclusion, plant operators are vital in implementing and executing preventative maintenance programs. Their daily tasks, such as visual inspections, monitoring equipment performance, cleaning, lubrication, calibration checks, and documentation, contribute to the overall effectiveness of the maintenance system. With their diverse skill set, including troubleshooting abilities, technical knowledge, familiarity with safety protocols, and understanding of plant-specific practices, plant operators play a crucial role in ensuring the reliability, longevity, and optimal performance of equipment.
Implementing a Preventative Maintenance Program
An effective preventative maintenance program requires careful planning and implementation. By following a systematic approach, plant operators can establish a robust maintenance plan tailored to the specific needs of their sludge management facility.
Preventative maintenance is crucial for ensuring the smooth operation of a sludge management facility. It helps prevent unexpected breakdowns, reduces downtime, and extends the lifespan of equipment. By taking proactive measures, plant operators can save time, money, and resources in the long run.
Steps to Develop a Maintenance Plan
The first step in developing a maintenance plan is to conduct a thorough equipment inventory and assessment. This involves identifying critical components, establishing maintenance intervals, and determining the necessary spare parts. By understanding the equipment's specifications and requirements, plant operators can develop a comprehensive maintenance strategy.
Once the inventory and assessment are complete, plant operators should create a calendarized maintenance schedule, ensuring tasks are evenly distributed throughout the year. This helps avoid overwhelming workloads during certain periods and ensures that all necessary maintenance activities are carried out in a timely manner.
Regular reviews and adjustments based on performance data and emerging trends are essential to keep the program optimized over time. By analyzing maintenance records, plant operators can identify patterns, spot potential issues, and make informed decisions to improve the effectiveness of the maintenance plan.
Tools and Equipment Needed
To execute preventative maintenance tasks effectively, plant operators require the right tools and equipment. This includes basic hand tools, such as wrenches, screwdrivers, and pliers, for general maintenance tasks. Precision measuring instruments, such as calipers and micrometers, are essential for accurate measurements and adjustments.
Lubricants and cleaning agents are necessary for equipment upkeep and to prevent corrosion and buildup. Plant operators should select the appropriate lubricants and cleaning agents based on the equipment manufacturer's recommendations to ensure compatibility and effectiveness.
Investing in reliable diagnostic equipment can significantly enhance maintenance efficiency and effectiveness. Vibration analyzers can detect and analyze equipment vibrations, helping identify potential issues before they escalate. Thermal imaging cameras can detect abnormal heat patterns, indicating potential overheating or electrical problems.
Furthermore, safety gear is essential to protect plant operators during maintenance activities. This includes gloves, safety glasses, ear protection, and appropriate clothing. Prioritizing safety is crucial to prevent accidents and injuries in the workplace.
In conclusion, implementing a preventative maintenance program is vital for the smooth operation of a sludge management facility. By following a systematic approach, conducting thorough equipment assessments, and using the right tools and equipment, plant operators can ensure the longevity and efficiency of their equipment. Regular reviews and adjustments based on performance data are essential to continuously optimize the maintenance plan. With a well-executed maintenance program, plant operators can minimize downtime, reduce costs, and maximize the overall performance of their sludge management facility.
Common Challenges in Preventative Maintenance
While preventative maintenance offers numerous benefits, plant operators often face certain challenges during its implementation and execution.
Preventative maintenance is a proactive approach that aims to prevent equipment failures and maximize the lifespan of assets. By regularly inspecting and maintaining equipment, plant operators can reduce downtime, increase productivity, and minimize repair costs. However, there are several challenges that need to be addressed to ensure the success of preventative maintenance programs.
Identifying Potential Problems
One of the primary challenges in preventative maintenance is accurately identifying potential problems before they lead to failures. This requires continuous monitoring, data analysis, and predictive maintenance techniques.
Continuous monitoring involves the use of sensors and monitoring systems to collect real-time data on equipment performance. By analyzing this data, plant operators can identify abnormal patterns or deviations from normal operating conditions, which may indicate potential issues.
Data analysis plays a crucial role in preventative maintenance. By utilizing advanced analytics tools, plant operators can analyze large volumes of data to identify patterns, trends, and correlations. This analysis can provide valuable insights into the health and condition of equipment, enabling operators to predict and prevent failures.
Predictive maintenance techniques, such as vibration analysis, thermography, and oil analysis, can also help in identifying potential problems. These techniques involve the use of specialized equipment to detect early warning signs of equipment deterioration or malfunction.
Implementing condition-based monitoring systems and utilizing advanced analytics tools can assist plant operators in detecting early warning signs and taking proactive measures promptly.
Overcoming Obstacles in Maintenance
Another common challenge is overcoming obstacles that hinder maintenance activities. These obstacles can include limited budgets, resource constraints, and time limitations.
Limited budgets often pose a challenge for plant operators when it comes to preventative maintenance. Allocating sufficient funds for equipment inspections, repairs, and replacement can be a daunting task. However, by demonstrating the cost-saving benefits of preventative maintenance, plant operators can secure the necessary budgetary support from management.
Resource constraints, such as a shortage of skilled technicians or lack of necessary tools and equipment, can also hinder maintenance activities. Plant operators can overcome this challenge by investing in training programs to enhance the skills of their maintenance staff. Additionally, establishing partnerships with external service providers can help fill resource gaps and ensure the timely completion of maintenance tasks.
Time limitations are another obstacle that plant operators often face. Balancing maintenance activities with production schedules and operational demands can be challenging. However, through effective prioritization, resource optimization, and collaboration with other departments, plant operators can mitigate these obstacles and ensure the timely completion of maintenance tasks.
In conclusion, preventative maintenance is a valuable strategy for plant operators to enhance equipment reliability and minimize downtime. However, it is essential to address the challenges associated with preventative maintenance, such as accurately identifying potential problems and overcoming obstacles in maintenance activities. By implementing the right tools, techniques, and strategies, plant operators can optimize their preventative maintenance programs and reap the benefits of improved equipment performance and reduced costs.
Safety Measures in Preventative Maintenance
Safety should be a top priority in any preventative maintenance program, especially in the sludge management industry. Plant operators must take necessary precautions to protect themselves and others while performing maintenance tasks.
One important aspect of safety in preventative maintenance is the implementation of safety protocols for plant operators. These protocols are designed to ensure the well-being of the operators and to minimize the risk of accidents or injuries. Plant operators should strictly adhere to established safety protocols, such as wearing appropriate personal protective equipment (PPE), following lockout/tagout procedures, and conducting proper risk assessments. By following these protocols, plant operators can significantly reduce the likelihood of accidents and create a safer working environment.
Regular safety training programs and ongoing safety audits also play a crucial role in maintaining a safe working environment. These programs provide plant operators with the necessary knowledge and skills to identify potential hazards and take appropriate measures to mitigate them. Ongoing safety audits help identify any gaps in the safety protocols and ensure that the necessary corrective actions are taken promptly. By continuously investing in safety training and audits, companies can demonstrate their commitment to the well-being of their employees and create a culture of safety within the organization.
Safety Protocols for Plant Operators
Plant operators play a vital role in the preventative maintenance process, and their safety is of utmost importance. To ensure their well-being, it is essential for plant operators to follow specific safety protocols.
One crucial safety protocol is the use of personal protective equipment (PPE). Plant operators should wear the appropriate PPE, such as helmets, gloves, safety glasses, and high-visibility vests, depending on the nature of the maintenance task. Wearing the correct PPE not only protects the operators from potential hazards but also helps create a safety-conscious work environment.
Another important safety protocol is the implementation of lockout/tagout procedures. These procedures ensure that equipment is properly shut down, isolated from energy sources, and tagged to indicate that maintenance work is being carried out. By following lockout/tagout procedures, plant operators can prevent accidental energization of equipment, which could lead to severe injuries or even fatalities.
Conducting proper risk assessments is also a critical safety protocol for plant operators. Before performing any maintenance task, operators should assess the potential risks involved and develop appropriate control measures to mitigate those risks. This proactive approach helps identify and address potential hazards before they can cause harm.
Handling Equipment Safely
When maintaining equipment, plant operators should ensure they are adequately trained in handling machinery and using specialized tools. Proper training not only enhances the efficiency of maintenance tasks but also minimizes the risk of accidents or damage to the equipment.
One aspect of safe equipment handling is following proper procedures for equipment isolation and de-energization. By isolating and de-energizing equipment before maintenance work, operators can eliminate the risk of accidental activation or release of stored energy. This precautionary measure significantly reduces the likelihood of accidents and ensures the safety of the operators.
Regular equipment inspections and maintenance are also essential for enhancing safety in the workplace. By conducting routine inspections, operators can identify any potential issues or worn-out components that may compromise the safety of the equipment or the operators. Timely replacement of worn-out components not only improves the performance of the equipment but also reduces the risk of accidents or breakdowns during operation.
In conclusion, safety is a critical aspect of preventative maintenance in the sludge management industry. By implementing and following safety protocols, providing regular training programs, and conducting safety audits, companies can create a safe working environment for plant operators. Additionally, proper equipment handling, including isolation and de-energization procedures, as well as regular inspections and maintenance, further enhance safety in the workplace. Prioritizing safety in preventative maintenance not only protects the well-being of the operators but also contributes to the overall success and efficiency of the maintenance program.
The Future of Preventative Maintenance in Sludge Management
The field of preventative maintenance is continuously evolving, with advancements in technology and a growing emphasis on sustainability shaping its future in the sludge management industry.
Technological Advancements and Their Impact
New technological solutions, such as Internet of Things (IoT) sensors, artificial intelligence (AI)-based analytics, and remote monitoring systems, offer plant operators unprecedented capabilities in preventative maintenance. These advancements enable real-time data collection, enhanced predictive abilities, and remote troubleshooting, leading to improved equipment reliability, reduced downtime, and greater operational efficiency.
Sustainability in Preventative Maintenance
Sustainability is gaining prominence in the sludge management industry, and preventative maintenance has a significant role to play in achieving sustainable practices. By optimizing equipment performance, minimizing resource consumption, and reducing waste generation, plant operators can contribute to a greener and more sustainable sludge management industry.
In conclusion, preventative maintenance is paramount for plant operators in the sludge management industry. By understanding its importance, fulfilling their role diligently, implementing effective maintenance programs, addressing common challenges, prioritizing safety, and embracing emerging trends, plant operators can optimize operations, ensure safety, and contribute to a sustainable future in the sludge management industry.