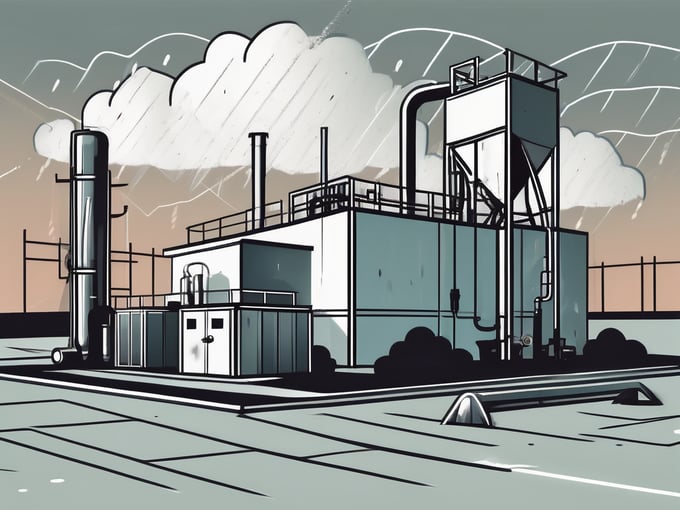
The Ultimate Guide to Preventative Maintenance for Plant Operators in the Stormwater Industry
In the stormwater industry, preventative maintenance plays a crucial role in ensuring the longevity and efficiency of plant operations. It involves proactive measures taken to identify and address potential issues before they escalate into major problems. By implementing a comprehensive maintenance program, plant operators can minimize downtime, reduce costs, and enhance safety. This ultimate guide explores the importance of preventative maintenance, essential practices, safety measures, training requirements, program implementation, and the future of maintenance in the stormwater industry.
Understanding the Importance of Preventative Maintenance
Preventative maintenance is a strategic approach that involves regular inspections, cleaning, and upkeep to prevent equipment failure and optimize performance. In the stormwater industry, where plants are exposed to harsh environmental conditions, the need for constant monitoring and maintenance is paramount. By investing time and resources into preventative maintenance, plant operators can minimize equipment breakdowns, improve system reliability, and extend the lifespan of their assets.
When it comes to stormwater treatment plants, the stakes are high. These plants play a crucial role in protecting our water bodies from pollution caused by runoff from rainfall. Without proper maintenance, these plants can become less effective in treating stormwater, leading to potential environmental contamination and regulatory violations.
The Role of Preventative Maintenance in the Stormwater Industry
In the stormwater industry, where runoff from rainfall can carry pollutants into water bodies, it is essential to ensure that stormwater treatment plants are operating at their full potential. Preventative maintenance plays a crucial role in identifying and preventing issues such as clogged filters, pump failures, and uncontrolled overflows. By addressing these problems proactively, plant operators can minimize the risk of environmental contamination and regulatory violations.
Regular inspections are a key component of preventative maintenance in the stormwater industry. These inspections involve carefully examining the various components of the treatment plant, including filters, pumps, and control systems. By conducting thorough inspections, operators can detect any signs of wear and tear, corrosion, or damage that may compromise the plant's performance.
Cleaning is another important aspect of preventative maintenance. Over time, stormwater treatment plants can accumulate debris, sediment, and other pollutants that can hinder their ability to effectively treat stormwater. Regular cleaning ensures that these plants are free from any obstructions, allowing them to operate at their optimal capacity.
Key Benefits of Regular Maintenance
Regular maintenance offers numerous benefits to plant operators in the stormwater industry. Firstly, it reduces the likelihood of equipment breakdowns, minimizing downtime and associated costs. When equipment fails, it not only disrupts the plant's operations but also requires immediate attention and repairs. By implementing preventative maintenance measures, operators can identify and address potential issues before they escalate into major problems, saving both time and money.
In addition to reducing equipment breakdowns, regular maintenance helps improve the overall efficiency of the plant. By ensuring that all components are in good working condition, preventative maintenance allows the plant to operate at its full potential. This, in turn, leads to optimal treatment performance and compliance with regulatory standards. Meeting these standards is not only essential for environmental protection but also for avoiding costly fines and penalties.
By identifying and addressing emerging issues early on, maintenance activities can prevent catastrophic failures. Imagine the consequences of a pump failure during a heavy rainstorm. The resulting overflow could lead to significant environmental damage and potential harm to nearby communities. Regular maintenance helps mitigate these risks by identifying and rectifying any potential problems before they have a chance to escalate.
Finally, regular maintenance promotes a safer work environment. Stormwater treatment plants can present various hazards, such as electrical issues, slippery surfaces, and exposure to harmful chemicals. By conducting regular inspections and maintenance, operators can address these potential hazards and ensure that all systems and equipment are functioning properly. This not only protects the workers but also contributes to the overall efficiency and productivity of the plant.
Essential Preventative Maintenance Practices
Implementing the following preventative maintenance practices is crucial for ensuring the smooth operation of stormwater treatment plants:
Routine Inspections and Their Importance
Regular inspections are the foundation of preventative maintenance. By conducting thorough visual assessments, operators can identify any signs of wear, damage, or potential failures. Key areas to inspect include pumps, valves, filtration systems, and electrical components. Inspections should also encompass the overall cleanliness of the plant and the performance of operational controls. By documenting and analyzing inspection data, operators can spot trends, make informed decisions, and address emerging issues promptly.
During routine inspections, operators should pay close attention to the condition of pumps. Pumps play a critical role in stormwater treatment plants, as they are responsible for moving water and other fluids throughout the system. Regular inspections can help identify any signs of wear on pump impellers, casings, or seals. Additionally, operators should inspect valves to ensure they are functioning properly and not leaking. Faulty valves can lead to inefficient water flow and potential system failures.
Another important aspect of routine inspections is evaluating the performance of filtration systems. Filtration plays a vital role in removing pollutants and sediments from stormwater before it is discharged. Operators should check filters for clogs or signs of deterioration, as these issues can compromise the effectiveness of the treatment process. Additionally, inspecting electrical components, such as control panels and wiring, is crucial to identify any potential hazards or malfunctions that could disrupt the operation of the plant.
Cleaning and Upkeep of Equipment
Cleaning and upkeep are vital to maintain the performance and integrity of equipment. This includes regular removal of debris, sediments, or pollutants from filters, screens, and drains. Operators should also ensure regular lubrication of moving parts and perform calibration checks on instruments. By implementing a thorough cleaning and upkeep regimen, operators can prevent build-up and inefficiencies, maximizing plant performance.
When it comes to cleaning filters, operators should follow manufacturer guidelines to ensure proper maintenance. This may involve backwashing filters to remove accumulated sediments or replacing filter media when it becomes excessively clogged. Screens should also be regularly cleaned to prevent blockages and maintain optimal water flow. Additionally, drains should be inspected and cleaned to prevent the accumulation of debris that could impede the drainage system.
Regular lubrication of moving parts is essential to reduce friction and prevent premature wear. Operators should use appropriate lubricants and follow manufacturer recommendations for lubrication intervals. Calibration checks on instruments, such as flow meters or pressure gauges, should be performed regularly to ensure accurate readings. Proper calibration is crucial for monitoring the performance of the stormwater treatment plant and detecting any deviations that may require adjustments or repairs.
Scheduling and Planning for Preventative Maintenance
An effective preventative maintenance program requires careful scheduling and planning. Operators should create a maintenance calendar to ensure regular and timely inspections and servicing. They should prioritize critical equipment and establish a proactive replacement strategy for components reaching the end of their lifespan. By planning maintenance activities in advance, operators can optimize their resources, minimize downtime, and prevent unplanned disruptions.
When creating a maintenance calendar, operators should consider the specific requirements of each piece of equipment. Some components may require more frequent inspections or servicing than others. By prioritizing critical equipment, operators can allocate their resources efficiently and focus on the areas that have the highest impact on the overall performance of the plant.
Establishing a proactive replacement strategy is essential to prevent unexpected failures and minimize downtime. By monitoring the lifespan of components, operators can plan for their replacement before they fail. This approach helps avoid costly emergency repairs and ensures that the stormwater treatment plant operates smoothly without interruptions.
Safety Measures in Preventative Maintenance
While performing preventative maintenance tasks, plant operators must prioritize safety to protect themselves and others. The following safety measures should be implemented:
Preventative maintenance plays a crucial role in ensuring the smooth operation of industrial plants and equipment. However, it is essential to recognize that maintenance tasks can pose potential risks to operators if proper safety measures are not followed. By adhering to specific safety protocols and utilizing personal protective equipment (PPE), operators can minimize the likelihood of accidents and injuries.
Personal Protective Equipment (PPE) for Maintenance Tasks
When conducting maintenance activities, operators should wear appropriate personal protective equipment (PPE), including gloves, safety glasses, and respiratory protection if necessary. PPE acts as a shield, providing a protective barrier between the operator and potential hazards. It minimizes the risk of injury from chemicals, noise, flying debris, or electrical hazards.
Proper selection and utilization of PPE are critical. Operators must ensure that the equipment they use is suitable for the specific maintenance task at hand. For instance, when handling corrosive substances, chemical-resistant gloves and goggles should be worn to prevent skin or eye irritation. Additionally, respiratory protection, such as masks or respirators, should be utilized when working in environments with airborne contaminants.
Regular inspection and maintenance of PPE are equally important. Operators should routinely check their equipment for any signs of damage or wear. If any defects or issues are detected, the PPE should be immediately replaced to maintain its effectiveness. By prioritizing the condition of their protective gear, operators can ensure their safety throughout the maintenance process.
Safe Protocols during Maintenance Operations
To ensure safety during maintenance operations, operators should follow established protocols. These protocols are designed to mitigate risks and prevent accidents. By adhering to these guidelines, operators can create a secure working environment for themselves and their colleagues.
One crucial protocol is the lockout/tagout procedure. This procedure involves isolating equipment from energy sources to prevent unexpected startup or release of stored energy. By following lockout/tagout protocols, operators can protect themselves from potential electrical or mechanical hazards. It is essential to undergo proper training on lockout/tagout procedures and strictly adhere to them during maintenance tasks.
Another important safety measure is ensuring proper ventilation when working with chemicals or in confined spaces. Adequate ventilation helps to minimize the risk of exposure to harmful fumes or gases, ensuring the well-being of operators. Properly ventilated work areas promote a healthier and safer environment for maintenance operations.
Safe handling of tools is also crucial in preventing accidents. Operators should be trained on the correct usage and storage of tools to minimize the risk of injuries. Regular maintenance and inspection of tools are necessary to identify any defects or malfunctions that could compromise safety.
Regular training sessions and refresher courses are vital to keep operators updated on safety protocols and best practices. By staying informed about the latest safety guidelines and techniques, operators can enhance their knowledge and skills, ensuring a safer work environment for all.
Training for Effective Preventative Maintenance
Plant operators play a critical role in ensuring the smooth operation and maintenance of equipment. To conduct effective preventative maintenance, they must possess essential skills and knowledge. The following training requirements are crucial:
Essential Skills for Plant Operators
Plant operators should be well-versed in various technical skills related to equipment operation and maintenance. This includes understanding electrical systems, basic plumbing, and troubleshooting techniques. By having a solid foundation in these areas, operators can efficiently identify and address any issues that may arise.
Moreover, plant operators should possess in-depth knowledge of stormwater treatment processes. This includes understanding the functions of pumps, filters, and chemical treatment systems. By comprehending the intricacies of these processes, operators can ensure that stormwater is effectively treated and meets the required quality standards.
Continuous skill development is vital for plant operators to keep up with emerging technologies and best practices. As technology advances, new equipment and maintenance strategies are introduced. Therefore, operators should actively seek opportunities to enhance their skills and stay up-to-date with the latest advancements in the industry.
Ongoing Training and Skill Development
To stay relevant in the ever-evolving stormwater industry, plant operators should engage in ongoing training and skill development. This can include attending industry conferences, webinars, and workshops to learn about new technologies and maintenance strategies.
Industry conferences provide a platform for operators to gain insights from experts in the field, exchange ideas with peers, and learn about innovative solutions to common challenges. Webinars offer the convenience of online learning, allowing operators to access valuable training materials from the comfort of their own facilities.
Additionally, workshops provide a hands-on learning experience where operators can practice their skills and receive guidance from experienced professionals. These interactive sessions foster a collaborative learning environment, enabling operators to learn from each other's experiences and share best practices.
Operators should also consider obtaining certifications relevant to their field. Certifications validate their knowledge and skills, making them more marketable and demonstrating their commitment to professional growth. Furthermore, certifications often require operators to engage in continuing education, ensuring that they stay updated with the latest industry standards and practices.
Participating in collaborative learning platforms, such as online forums or industry-specific communities, is another valuable way for operators to expand their knowledge. These platforms provide a space for operators to ask questions, share experiences, and learn from the collective wisdom of their peers.
In conclusion, training for effective preventative maintenance is essential for plant operators. By possessing essential skills, engaging in ongoing training, and participating in collaborative learning, operators can ensure that they are well-equipped to handle the challenges of equipment operation and maintenance in the stormwater industry.
Implementing a Preventative Maintenance Program
To develop and implement an effective preventative maintenance program, follow these steps:
Steps to Develop a Maintenance Plan
Begin by conducting a comprehensive assessment of your plant's current maintenance practices. Identify areas for improvement and set performance goals. Develop a maintenance plan that includes a schedule for routine inspections, cleaning activities, and servicing of equipment. Establish protocols for documenting maintenance activities and tracking equipment performance. Regularly review and revise the maintenance plan based on feedback and changing needs.
Monitoring and Evaluating the Maintenance Program
Periodically monitor and evaluate the effectiveness of your maintenance program. Collect data on equipment performance, maintenance costs, and downtime. Analyze this data to identify patterns or areas for improvement. Make adjustments to your maintenance plan as necessary to optimize efficiency and minimize disruptions.
The Future of Preventative Maintenance in the Stormwater Industry
The stormwater industry is evolving, and so are maintenance practices. Technological advancements are driving innovation and introducing new tools to enhance preventative maintenance. For example, sensor-based monitoring systems can provide real-time data on equipment performance, enabling predictive maintenance. Artificial intelligence and machine learning algorithms can optimize maintenance schedules based on historical trends and usage patterns. Additionally, the industry is increasingly emphasizing sustainability in maintenance practices, aiming to reduce waste and energy consumption.
Technological Advancements in Maintenance Practices
Technological advancements are revolutionizing maintenance practices in the stormwater industry. Remote monitoring systems, Internet of Things (IoT) devices, and advanced analytics are being employed to monitor equipment performance and detect anomalies. Robotic systems are being developed to automate routine maintenance tasks, minimizing human intervention and increasing efficiency. These advancements promise to streamline maintenance operations and improve overall plant performance.
Sustainability and Preventative Maintenance
Sustainability is gaining prominence in the stormwater industry, and maintenance practices are no exception. Plant operators are adopting eco-friendly approaches that minimize waste, reduce chemical usage, and optimize energy consumption. For example, green solutions such as rainwater harvesting or natural filtration techniques are being incorporated into maintenance programs. By prioritizing sustainability, operators can not only reduce environmental impact but also improve the cost-effectiveness of their maintenance operations.
By understanding the importance of preventative maintenance, implementing essential practices, prioritizing safety, investing in training, and embracing technological advancements, plant operators can elevate their maintenance programs to new heights. This comprehensive guide serves as a roadmap for those navigating the stormwater industry and aims to empower operators to optimize the performance and reliability of their plant operations through effective preventative maintenance.