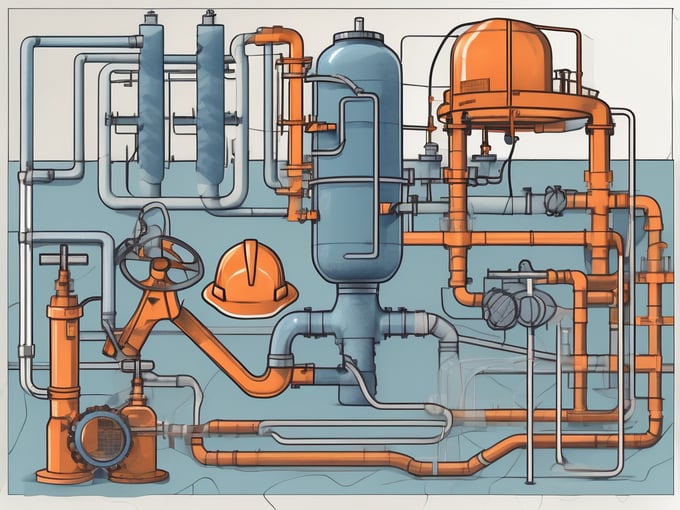
The Ultimate Guide to Preventative Maintenance for Specifying Engineers in the Wastewater Industry
In the wastewater industry, preventative maintenance plays a crucial role in ensuring the smooth operation of equipment and the efficiency of treatment processes. Specifying engineers, in particular, have a significant responsibility in this domain. By understanding the importance of preventative maintenance and implementing effective strategies, specifying engineers can contribute to prolonging the lifespan of wastewater equipment, increasing reliability, and reducing downtime.
Understanding the Importance of Preventative Maintenance in the Wastewater Industry
The wastewater industry relies on numerous components and systems to treat and manage wastewater effectively. From pumps and valves to filtration systems and chemical dosing equipment, each element plays a vital role in the treatment process. Any failure or breakdown in these critical systems can lead to process disruptions, increased maintenance costs, and even environmental hazards. This is where preventative maintenance comes into play.
Preventative maintenance involves regular inspections, servicing, and repairs to ensure that equipment and systems are operating at their optimal level. By implementing a proactive approach to maintenance, the wastewater industry can prevent costly breakdowns, extend the lifespan of equipment, and maintain the efficiency of treatment processes.
The Role of Specifying Engineers in Maintenance
Specifying engineers are responsible for designing wastewater treatment systems and selecting the most appropriate equipment for specific applications. They play a crucial role in ensuring that systems are reliable, efficient, and meet regulatory requirements. However, their responsibilities don't end there. Specifying engineers must also consider the long-term maintenance and operation of these systems when making equipment choices.
By specifying equipment with preventative maintenance in mind, engineers can simplify maintenance procedures, optimize equipment performance, and reduce the overall lifecycle cost of wastewater treatment systems.
For example, when selecting pumps for a wastewater treatment plant, specifying engineers can choose models that are designed for easy maintenance. These pumps may have features such as quick-disconnect fittings, accessible lubrication points, and built-in diagnostic systems that can help identify potential issues before they cause major failures. By considering these factors during the design phase, engineers can ensure that maintenance tasks are streamlined and efficient.
Key Benefits of Preventative Maintenance
Preventative maintenance offers several key benefits in the wastewater industry. Firstly, it helps detect and address potential issues before they escalate into major problems. By conducting regular inspections, performing routine cleaning, and replacing worn-out parts as necessary, maintenance professionals can identify and resolve minor issues, preventing them from becoming major failures that can result in costly repairs and prolonged downtimes.
For instance, during a routine inspection of a filtration system, maintenance technicians may discover a small leak in one of the pipes. By promptly repairing the leak and replacing the damaged section, they prevent the leak from worsening and potentially causing a system failure. This proactive approach saves time, money, and resources that would have been required to address a larger problem.
Secondly, preventative maintenance helps extend the lifespan of wastewater equipment. By adhering to manufacturer-recommended maintenance schedules and performing timely repairs, engineers can ensure that equipment operates within its intended design parameters, reducing wear and tear and increasing longevity.
Regular maintenance tasks such as lubrication, calibration, and cleaning can significantly impact the lifespan of equipment. For example, by regularly lubricating the moving parts of pumps and valves, engineers can reduce friction and wear, preventing premature failure and extending the lifespan of these components.
Additionally, preventative maintenance enhances the reliability and efficiency of wastewater treatment systems. Regular servicing helps optimize equipment performance, minimize energy consumption, and maximize the effectiveness of the treatment process. This not only reduces operational costs but also helps meet regulatory requirements and maintain compliance with environmental standards.
By regularly inspecting and cleaning filtration systems, engineers can ensure that they are operating at their optimal level, removing contaminants effectively and minimizing the strain on downstream processes. This improves the overall efficiency of the treatment plant and reduces the energy required for wastewater treatment.
Overall, implementing a robust preventative maintenance program can deliver cost savings, minimize disruptions, and ensure the longevity and optimal performance of wastewater treatment systems. By prioritizing maintenance and investing in regular inspections and repairs, the wastewater industry can continue to provide effective and sustainable wastewater treatment solutions.
Fundamental Concepts of Preventative Maintenance
Before diving into the specifics of implementing preventative maintenance strategies, it's essential to understand the fundamental concepts that underpin this approach.
Preventative maintenance refers to a systematic approach to ensure the ongoing functionality and reliability of equipment by performing regular inspections, maintenance tasks, and repairs. It involves scheduled activities aimed at preventing equipment failures and minimizing the impact of unexpected breakdowns.
This approach is based on the idea that it is more efficient and cost-effective to prevent problems proactively, rather than waiting for them to occur and then responding reactively to repair them.
Implementing preventative maintenance strategies can have several benefits for organizations. Firstly, it helps to reduce the risk of equipment failure, which can lead to costly downtime and production losses. By regularly inspecting and maintaining equipment, potential issues can be identified and addressed before they escalate into major problems.
Secondly, preventative maintenance can improve the overall performance and efficiency of equipment. Regular cleaning, lubrication, and calibration can ensure that equipment operates at its optimal level, resulting in improved productivity and reduced energy consumption.
Furthermore, preventative maintenance can extend the useful life of equipment. By taking proactive measures to prevent wear and tear, equipment components can be preserved, reducing the need for frequent replacements and saving on replacement costs.
Defining Preventative Maintenance
Preventative maintenance refers to a systematic approach to ensure the ongoing functionality and reliability of equipment by performing regular inspections, maintenance tasks, and repairs. It involves scheduled activities aimed at preventing equipment failures and minimizing the impact of unexpected breakdowns.
This approach is based on the idea that it is more efficient and cost-effective to prevent problems proactively, rather than waiting for them to occur and then responding reactively to repair them.
Implementing preventative maintenance strategies can have several benefits for organizations. Firstly, it helps to reduce the risk of equipment failure, which can lead to costly downtime and production losses. By regularly inspecting and maintaining equipment, potential issues can be identified and addressed before they escalate into major problems.
Secondly, preventative maintenance can improve the overall performance and efficiency of equipment. Regular cleaning, lubrication, and calibration can ensure that equipment operates at its optimal level, resulting in improved productivity and reduced energy consumption.
Furthermore, preventative maintenance can extend the useful life of equipment. By taking proactive measures to prevent wear and tear, equipment components can be preserved, reducing the need for frequent replacements and saving on replacement costs.
The Lifecycle of Wastewater Equipment
All equipment in the wastewater industry follows a lifecycle that includes various stages: design, procurement, installation, operation, and maintenance. Each stage has its unique considerations, and maintenance plays a critical role throughout the entire lifecycle.
During the design and procurement stages, specifying engineers must ensure that the selected equipment is suitable for the intended application and aligns with the maintenance resources available. Properly documenting equipment requirements and maintenance procedures during these stages can greatly simplify future maintenance efforts.
Once installed and operational, equipment requires regular maintenance to prevent deterioration, ensure optimal performance, and extend its useful life. Effective maintenance encompasses routine tasks such as inspections, lubrication, calibration, and cleaning, as well as more in-depth repairs and component replacements when necessary.
By considering the lifecycle of wastewater equipment, specifying engineers can develop comprehensive maintenance plans that address the specific needs and challenges associated with each stage.
For example, during the design stage, engineers can evaluate different equipment options and select those that are known for their reliability and ease of maintenance. They can also collaborate with maintenance personnel to understand their requirements and incorporate them into the equipment specifications.
During the procurement stage, engineers can work closely with suppliers to ensure that the selected equipment meets all the necessary standards and specifications. They can also negotiate service contracts that include regular maintenance visits and spare parts availability.
Once the equipment is installed and operational, maintenance activities become crucial to its performance and longevity. Regular inspections can help identify any signs of wear or potential issues that need to be addressed. Lubrication and calibration tasks can be performed to ensure that the equipment operates at its optimal level. Cleaning procedures can be implemented to prevent the buildup of debris or contaminants that could affect the equipment's performance.
In addition to routine maintenance tasks, more in-depth repairs and component replacements may be required over time. By closely monitoring the equipment's performance and addressing any issues promptly, engineers can minimize the impact of unexpected breakdowns and extend the useful life of the equipment.
Overall, understanding the lifecycle of wastewater equipment and incorporating maintenance considerations throughout each stage can help organizations develop effective and comprehensive preventative maintenance strategies.
Implementing Preventative Maintenance Strategies
Implementing an effective preventative maintenance strategy involves several key steps. By following a systematic approach, specifying engineers can develop and execute a plan that suits the unique requirements of their wastewater treatment systems.
Preventative maintenance is crucial in ensuring the smooth operation of wastewater treatment systems. It helps to prevent unexpected breakdowns, reduces the risk of costly repairs, and extends the lifespan of equipment. Let's explore the steps involved in developing a preventative maintenance plan in more detail.
Steps to Develop a Preventative Maintenance Plan
The first step in developing a preventative maintenance plan is to conduct a comprehensive equipment inventory. This involves identifying all critical components, their location, and their functional dependencies within the wastewater treatment system. By having a clear picture of the equipment landscape, specifying engineers can determine the scope of maintenance activities required.
During the equipment inventory process, engineers may discover hidden components or overlooked equipment that require maintenance. This thorough examination ensures that no equipment is left unattended, reducing the risk of unexpected failures.
Next, engineers must establish maintenance schedules for each piece of equipment. This includes defining the frequency of inspections, cleaning, lubrication, calibration, and any other maintenance tasks specific to the equipment in question. These schedules should consider factors such as equipment runtime, manufacturer recommendations, and regulatory requirements.
By establishing maintenance schedules, engineers can ensure that each piece of equipment receives the necessary attention at the right time. This proactive approach minimizes the likelihood of equipment failure and maximizes operational efficiency.
It is also crucial to document maintenance procedures and establish clear guidelines for technicians to follow. This documentation should include step-by-step instructions, safety precautions, troubleshooting tips, and any special considerations for the equipment being maintained.
Clear and detailed documentation is essential in ensuring consistency and accuracy in maintenance activities. It provides technicians with the necessary information to perform tasks correctly and safely, reducing the risk of errors or accidents.
Once the plan is developed, it is crucial to allocate adequate resources, including skilled personnel, tools, and spare parts, to execute the maintenance tasks effectively. Regular training and knowledge sharing sessions should also be conducted to ensure that maintenance technicians stay up to date with best practices and industry developments.
Having the right resources and trained personnel is vital in implementing a preventative maintenance plan successfully. Skilled technicians equipped with the necessary tools and spare parts can carry out maintenance tasks efficiently, minimizing downtime and maximizing system performance.
Tools and Technologies for Preventative Maintenance
In addition to developing a comprehensive plan, leveraging appropriate tools and technologies can further enhance the effectiveness of preventative maintenance strategies.
One essential tool is a computerized maintenance management system (CMMS), which helps schedule and track maintenance activities, manage work orders, and store equipment documentation. A CMMS allows engineers and technicians to streamline maintenance operations, ensure accountability, and generate reports for analysis and decision-making.
With a CMMS in place, engineers can easily track maintenance tasks, monitor progress, and generate reports to evaluate the effectiveness of the preventative maintenance program. This data-driven approach enables continuous improvement and optimization of maintenance activities.
Other technologies, such as sensors and condition monitoring systems, can provide real-time insights into equipment performance, enabling early detection of abnormalities and predictive maintenance practices. These technologies alert maintenance personnel to potential issues before they cause severe damage or failure, allowing for timely intervention and preventing costly downtime.
Sensors and condition monitoring systems offer a proactive approach to maintenance by continuously monitoring equipment performance. They provide real-time data on factors like temperature, vibration, and fluid levels, allowing engineers to detect anomalies and take corrective actions promptly. This predictive maintenance approach helps to prevent unexpected breakdowns and optimize maintenance schedules.
Implementing preventative maintenance strategies requires careful planning, documentation, resource allocation, and the use of appropriate tools and technologies. By following these steps and leveraging the right resources, specifying engineers can ensure the long-term reliability and efficiency of wastewater treatment systems.
Overcoming Challenges in Preventative Maintenance
While preventative maintenance brings numerous benefits, there are unique challenges that specifying engineers may encounter in the wastewater industry.
Common Obstacles in Wastewater Industry Maintenance
One common challenge is the harsh operating conditions often found in wastewater treatment plants. Corrosion, abrasion, and exposure to various chemicals can accelerate equipment deterioration and complicate maintenance efforts. Engineers must consider these factors when selecting equipment and develop maintenance plans that address the specific challenges associated with these conditions.
Another challenge is the scarcity of skilled maintenance personnel in the industry. Finding technicians with the right expertise and experience in wastewater treatment equipment can be a daunting task. Engineers must invest in training programs, cross-functional knowledge sharing, and developing maintenance procedures that are easy to follow by technicians with different backgrounds and skill levels.
Solutions for Maintenance Challenges
To overcome the challenges in preventative maintenance, specifying engineers can implement several strategies. Choosing equipment made with corrosion-resistant materials and coatings can minimize the impact of harsh operating conditions and extend equipment life. Regular monitoring of equipment performance and condition can help catch issues before they escalate, allowing for timely repairs.
Collaboration and knowledge sharing among maintenance professionals in the industry can also play a significant role in overcoming challenges. By connecting with peers, participating in industry events and conferences, and leveraging online forums and communities, engineers can stay updated on the latest maintenance strategies, technologies, and solutions.
Future Trends in Preventative Maintenance
As the wastewater industry continues to evolve and embrace technological advancements, several future trends are shaping the landscape of preventative maintenance.
Innovations in Maintenance Strategies
Emerging technologies, such as artificial intelligence (AI), big data analytics, and the Internet of Things (IoT), are revolutionizing maintenance practices. AI algorithms can analyze massive amounts of data to predict when equipment failures may occur and suggest suitable maintenance actions. IoT-enabled sensors and devices can provide real-time insights and automate data collection, enabling more accurate condition monitoring and predictive maintenance.
Adopting these technologies can allow specifying engineers to move from scheduled maintenance to condition-based or predictive maintenance approaches, reducing operational costs, and minimizing unnecessary downtime.
The Impact of Regulations on Preventative Maintenance
Increasingly stringent regulations and environmental standards are also influencing preventative maintenance practices in the wastewater industry. Engineers must stay informed about the latest regulations and ensure that maintenance plans align with these requirements. By embracing a proactive approach to compliance, engineers can avoid penalties, maintain public trust, and contribute to a healthier and more sustainable environment.
In conclusion, preventative maintenance is a fundamental aspect of ensuring smooth operations and optimal performance in the wastewater industry. Specifying engineers play a crucial role in designing equipment and systems with maintenance in mind, implementing comprehensive maintenance plans, and overcoming the challenges that arise. By staying ahead of industry trends and leveraging innovative technologies, engineers can drive the future of preventative maintenance, delivering significant benefits to wastewater treatment systems and the environment as a whole.