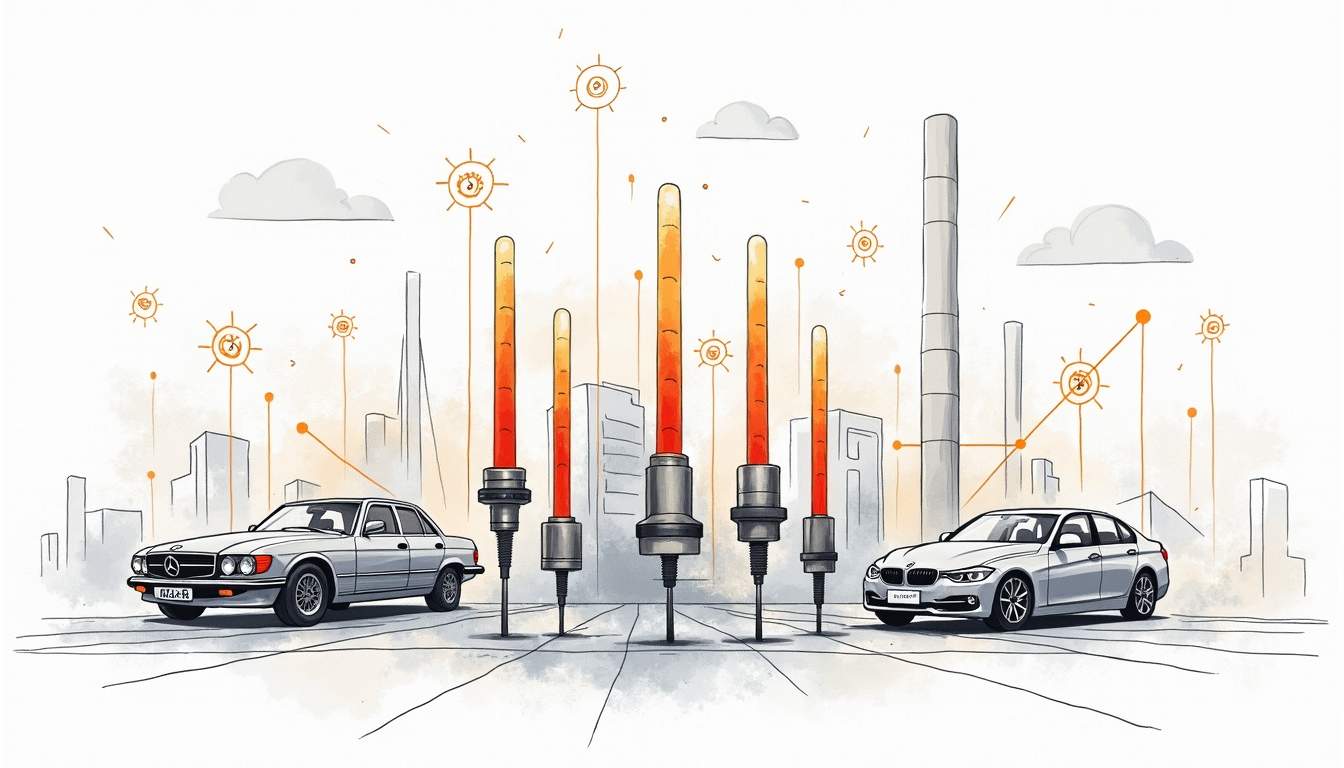
Top High Temperature Sensors: Features, Applications, and Innovations
High temperature sensors play a crucial role in various industries, from manufacturing to aerospace. As technology advances, the demand for accurate and reliable temperature measurement in extreme conditions has grown significantly. This article explores the leading high temperature sensors, their features, applications, and the latest innovations driving the market forward.
Understanding High Temperature Sensors
High temperature sensors are devices designed to measure temperature in environments where traditional sensors may fail. These sensors can withstand extreme conditions, making them essential in industries such as metallurgy, automotive, and energy. Their ability to function effectively at elevated temperatures ensures safety, efficiency, and reliability in various applications. In addition to their robust construction, high temperature sensors often incorporate advanced technologies that enhance their performance, such as digital signal processing and wireless communication capabilities, which facilitate remote monitoring and data collection.
Types of High Temperature Sensors
There are several types of high temperature sensors, each suited for specific applications. The most common types include thermocouples, resistance temperature detectors (RTDs), and infrared sensors. Thermocouples, for instance, are widely used due to their simple construction and ability to measure a broad range of temperatures. RTDs, on the other hand, provide high accuracy and stability, making them ideal for applications requiring precise temperature measurements. Infrared sensors offer non-contact measurement, which is particularly useful in scenarios where the sensor cannot be physically placed in the high-temperature environment, such as monitoring molten metal or hot gases. Understanding the differences between these types can help in selecting the right sensor for a particular application.
Key Features of High Temperature Sensors
High temperature sensors are characterized by their ability to operate in harsh environments. Key features include:
- Temperature Range: Many high temperature sensors can measure temperatures exceeding 1000°C, making them suitable for extreme applications.
- Durability: These sensors are often constructed from robust materials, such as ceramics or specialized alloys, to withstand harsh conditions.
- Response Time: Quick response times are essential for real-time monitoring and control in industrial processes.
Additionally, high temperature sensors often feature advanced calibration techniques that enhance their accuracy over time. Some models are equipped with self-diagnostic capabilities, allowing them to identify potential issues before they lead to failure. This proactive approach not only improves the longevity of the sensors but also ensures that critical processes remain uninterrupted. Furthermore, many modern high temperature sensors are designed to integrate seamlessly with existing automation systems, enabling enhanced data analytics and process optimization, which are crucial in today’s competitive industrial landscape.
Applications of High Temperature Sensors
The applications of high temperature sensors are vast and varied, reflecting their importance across multiple sectors. From monitoring industrial processes to ensuring safety in hazardous environments, these sensors are indispensable.
Industrial Manufacturing
In industrial manufacturing, high temperature sensors are used to monitor processes such as metal forging, casting, and welding. Precise temperature control is critical in these processes to ensure product quality and prevent defects. Sensors help maintain optimal temperatures, leading to increased efficiency and reduced waste. Furthermore, these sensors are integral in the production of ceramics and glass, where temperature fluctuations can lead to significant variations in material properties. By providing real-time data, manufacturers can make informed adjustments, thereby enhancing the durability and performance of the final products.
Aerospace and Defense
The aerospace industry relies heavily on high temperature sensors for engine monitoring and testing. These sensors provide vital data on engine performance and safety, ensuring that aircraft operate within safe temperature limits. Additionally, they are used in various defense applications, where reliability and accuracy are paramount. In missile systems and spacecraft, high temperature sensors monitor critical components during extreme conditions, such as re-entry into the atmosphere. Their ability to function accurately in such demanding environments not only enhances mission success rates but also contributes to the development of next-generation aerospace technologies.
Energy Sector
In the energy sector, high temperature sensors are essential for monitoring power generation systems, including gas turbines and nuclear reactors. These sensors help manage thermal efficiency and safety, contributing to the overall effectiveness of energy production. Their ability to withstand extreme conditions is vital for maintaining operational integrity. Moreover, in renewable energy applications, such as concentrated solar power plants, high temperature sensors play a crucial role in optimizing the heat transfer processes. By ensuring that temperatures are maintained within the desired range, these sensors help maximize energy output and improve the sustainability of energy solutions, paving the way for a greener future.
Innovations in High Temperature Sensor Technology
As industries evolve, so too does the technology behind high temperature sensors. Recent innovations have enhanced their performance, accuracy, and reliability, paving the way for new applications and improved processes.
Wireless Technology
One of the most significant advancements in high temperature sensors is the integration of wireless technology. Wireless sensors eliminate the need for cumbersome wiring, allowing for easier installation and maintenance. This innovation is particularly beneficial in hard-to-reach areas, where traditional sensors may be challenging to deploy. Moreover, the reduction of wiring not only simplifies the installation process but also minimizes the risk of damage to cables in extreme environments, which can lead to costly downtimes and repairs. As industries increasingly adopt automation and smart technologies, wireless high temperature sensors are becoming indispensable in sectors such as aerospace, automotive, and energy production.
Smart Sensors and IoT Integration
The rise of the Internet of Things (IoT) has transformed high temperature sensors into smart devices. These sensors can now communicate data in real-time, enabling remote monitoring and advanced analytics. This capability allows industries to optimize processes, predict failures, and enhance overall operational efficiency. For instance, in manufacturing, real-time data from smart sensors can help identify temperature fluctuations that may indicate equipment malfunctions, allowing for proactive maintenance before a failure occurs. Additionally, the integration of machine learning algorithms with these sensors can lead to predictive analytics, where historical data is analyzed to forecast future performance trends, further improving decision-making processes.
Advanced Materials and Coatings
Innovations in materials science have led to the development of advanced coatings that improve the durability and performance of high temperature sensors. These coatings can enhance resistance to oxidation, corrosion, and thermal shock, extending the lifespan of sensors and reducing maintenance costs. Furthermore, the use of nanotechnology in sensor design has opened up new possibilities for creating sensors that can withstand extreme conditions while maintaining high levels of accuracy. For example, sensors designed with nanostructured materials can provide improved thermal conductivity and faster response times, making them ideal for applications in industries such as petrochemical refining and metal processing, where precision is critical. As research continues, we can expect even more breakthroughs in materials that will further push the boundaries of high temperature sensor technology.
Choosing the Right High Temperature Sensor
Selecting the appropriate high temperature sensor for a specific application requires careful consideration of several factors. Understanding these factors can help ensure optimal performance and reliability.
Temperature Range Requirements
The first step in choosing a high temperature sensor is to determine the temperature range required for the application. Different sensors have varying temperature limits, so it is crucial to select one that can operate effectively within the specific range needed. For instance, thermocouples are often favored for extreme temperatures, as they can measure from -200°C to over 2000°C, depending on their type. On the other hand, RTDs (Resistance Temperature Detectors) are typically used for more moderate ranges, usually up to around 850°C, but they offer superior accuracy and stability within that range. Understanding the specific temperature dynamics of your application will guide you in making the right choice.
Environmental Conditions
Consideration of the environmental conditions where the sensor will be used is also essential. Factors such as humidity, pressure, and the presence of corrosive substances can impact sensor performance. Selecting a sensor designed to withstand these conditions will ensure reliable operation. For example, if the sensor is to be used in a high-humidity environment, it may be necessary to choose a sensor with a protective coating or one that is hermetically sealed to prevent moisture ingress. Additionally, in applications where sensors are exposed to dust, dirt, or other particulates, the design should incorporate features that prevent clogging or interference with the sensor's readings. Understanding these environmental challenges will help in selecting a sensor that not only meets the temperature requirements but also thrives in its operating conditions.
Calibration and Accuracy
Calibration is another critical aspect to consider. High temperature sensors must provide accurate readings to ensure safety and efficiency. It is essential to choose sensors that offer high accuracy and can be calibrated easily to maintain performance over time. Regular calibration is necessary to account for any drift in sensor readings, especially in high temperature applications where materials can expand or degrade. Furthermore, some sensors come with built-in self-calibration features, which can significantly reduce downtime and maintenance efforts. It is also advisable to review the manufacturer's specifications for accuracy and repeatability, as these metrics will directly affect the reliability of your measurements and, consequently, the overall safety of your operation.
Future Trends in High Temperature Sensors
The future of high temperature sensors looks promising, with several trends shaping the market. As industries continue to evolve, the demand for more advanced and reliable temperature measurement solutions will only increase.
Sustainability and Energy Efficiency
As the world moves towards more sustainable practices, high temperature sensors will play a vital role in enhancing energy efficiency. By providing accurate temperature readings, these sensors can help industries optimize their processes and reduce energy consumption, contributing to a greener future. For instance, in manufacturing processes where heat is a critical factor, precise temperature control can lead to significant reductions in waste and emissions. This not only benefits the environment but also helps companies comply with increasingly stringent regulations aimed at reducing carbon footprints.
Enhanced Data Analytics
The integration of advanced data analytics with high temperature sensors will enable industries to gain deeper insights into their operations. By analyzing temperature data, companies can identify trends, predict failures, and make informed decisions to improve efficiency and reduce costs. Moreover, the use of machine learning algorithms can enhance predictive maintenance strategies, allowing for timely interventions before equipment failures occur. This proactive approach not only minimizes downtime but also extends the lifespan of machinery, resulting in substantial cost savings over time.
Miniaturization and Integration
Miniaturization of high temperature sensors is another trend that is likely to continue. Smaller sensors can be integrated into various systems, allowing for more comprehensive monitoring and control. This trend will enhance the versatility of high temperature sensors, making them suitable for a broader range of applications. For example, in the aerospace sector, miniaturized sensors can be embedded into engine components, providing real-time data that can improve performance and safety. Additionally, the integration of these sensors with IoT technology will facilitate remote monitoring and data collection, enabling smarter, more responsive industrial environments.
Advancements in Materials
Another significant trend is the development of advanced materials for high temperature sensors. New materials, such as ceramics and specialized alloys, are being researched to withstand extreme conditions while maintaining accuracy and reliability. These advancements not only improve the durability of sensors but also expand their operational range, making them suitable for use in industries such as aerospace, automotive, and energy production. The ability to withstand higher temperatures without degradation opens up new possibilities for innovation in sensor design and application.
Wireless Technology Integration
The integration of wireless technology into high temperature sensors is also gaining traction. Wireless sensors can provide greater flexibility in installation and reduce the need for cumbersome wiring, which is particularly advantageous in hard-to-reach or hazardous environments. This technology allows for real-time data transmission, enabling immediate responses to temperature fluctuations. As industries increasingly adopt smart technologies, the demand for wireless high temperature sensors is expected to grow, facilitating the transition towards fully automated and interconnected systems.
Conclusion
High temperature sensors are essential components in many industries, providing critical data for safety, efficiency, and performance. With advancements in technology and materials, these sensors are becoming more reliable and versatile. As industries continue to evolve, the demand for high temperature sensors will grow, driving innovation and enhancing operational capabilities.
Understanding the features, applications, and innovations of high temperature sensors is crucial for making informed decisions. By choosing the right sensor for specific applications, industries can ensure optimal performance and contribute to a more sustainable future.