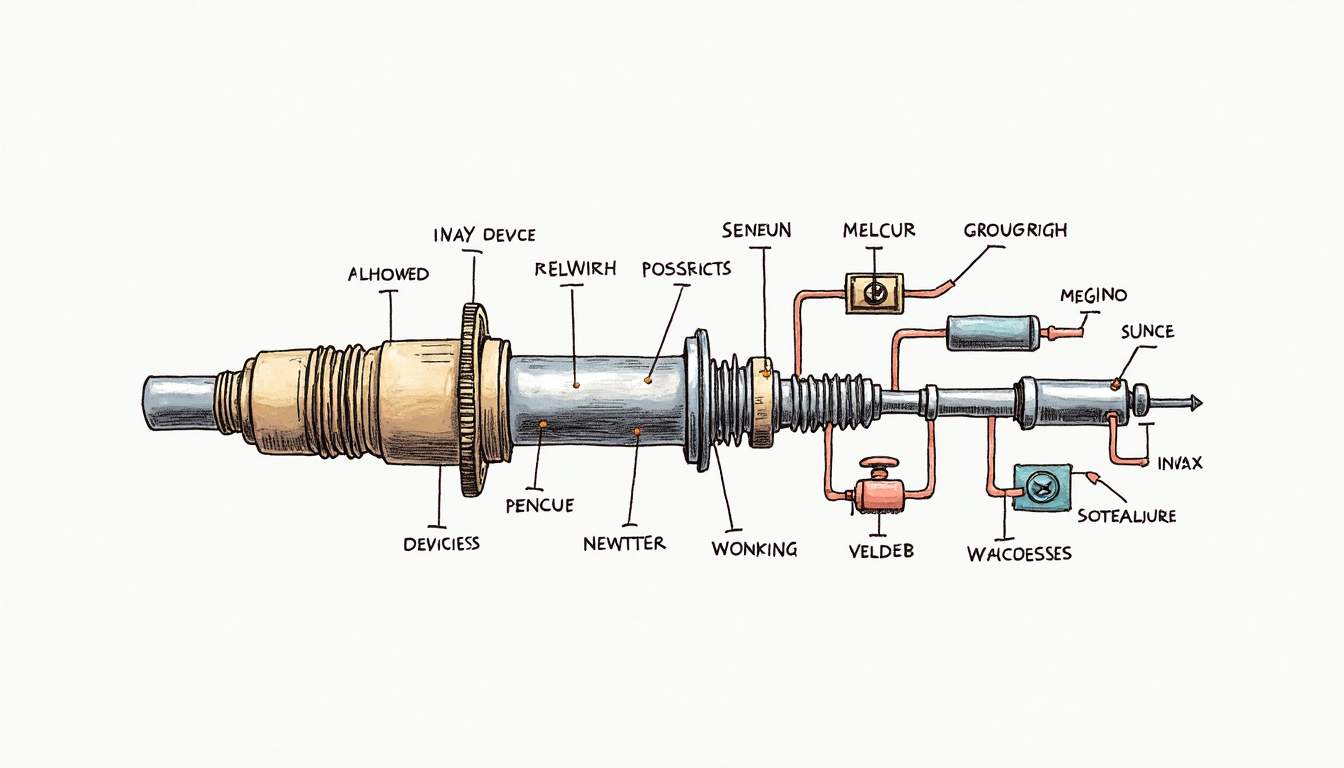
Understanding DP Sensors: Functionality, Applications, and Benefits
In the ever-evolving landscape of industrial automation and process control, differential pressure (DP) sensors play a crucial role. These sensors are essential for measuring the pressure difference between two points, providing valuable insights into various processes and systems. This article delves into the functionality, applications, and benefits of DP sensors, shedding light on why they are indispensable in modern industries.
What is a Differential Pressure Sensor?
A differential pressure sensor is a device that measures the difference in pressure between two points in a system. This measurement is vital for monitoring and controlling processes in various applications, from HVAC systems to chemical manufacturing. By understanding the pressure differential, operators can make informed decisions to optimize performance and ensure safety. In industries such as pharmaceuticals and food processing, maintaining precise pressure differentials is crucial not only for operational efficiency but also for compliance with stringent regulatory standards. A small deviation in pressure can lead to significant impacts on product quality and safety, highlighting the importance of reliable differential pressure measurement.
How DP Sensors Work
DP sensors operate based on the principle of measuring the pressure at two different points. These sensors typically consist of two pressure ports, which are connected to the points of interest. The sensor calculates the pressure difference and converts it into an electrical signal that can be easily interpreted by control systems. This conversion process allows for real-time monitoring and adjustments, enabling systems to respond dynamically to changes in pressure conditions. Additionally, many modern DP sensors are equipped with digital interfaces, allowing for seamless integration with advanced data acquisition systems, enhancing the overall monitoring capabilities.
Most DP sensors use piezoelectric or capacitive technology to detect pressure changes. The choice of technology often depends on the specific application and the required accuracy. For example, piezoelectric sensors are known for their rapid response times, making them ideal for dynamic applications, while capacitive sensors offer high stability for static measurements. Furthermore, some sensors incorporate temperature compensation features to ensure accuracy across varying environmental conditions, making them suitable for a wide range of industrial settings.
Types of DP Sensors
There are several types of differential pressure sensors available in the market, each designed for specific applications. Some common types include:
- Absolute Pressure Sensors: Measure pressure relative to a perfect vacuum.
- Gauge Pressure Sensors: Measure pressure relative to atmospheric pressure.
- Sealed Pressure Sensors: Similar to gauge sensors but sealed to prevent atmospheric pressure influence.
Understanding the differences between these types is crucial for selecting the right sensor for a given application. Choosing the appropriate sensor ensures accurate measurements and optimal performance. Additionally, there are specialized DP sensors designed for extreme environments, such as high-temperature or corrosive conditions, which utilize robust materials and advanced sealing technologies to maintain functionality and reliability. These specialized sensors are essential in industries like oil and gas, where equipment must withstand harsh operational conditions while providing precise measurements.
Applications of Differential Pressure Sensors
DP sensors are widely used across various industries due to their versatility and reliability. Their applications range from simple pressure monitoring to complex process control systems. Below are some key industries where DP sensors are commonly employed.
HVAC Systems
In heating, ventilation, and air conditioning (HVAC) systems, DP sensors are essential for monitoring airflow and maintaining optimal indoor air quality. By measuring the pressure difference across filters, fans, and ductwork, these sensors help ensure efficient operation and energy savings.
For instance, a DP sensor can detect when air filters are clogged, prompting maintenance before airflow is significantly affected. This proactive approach not only enhances system performance but also extends the life of HVAC equipment. Additionally, these sensors can play a crucial role in balancing air distribution throughout a building, ensuring that every room receives adequate ventilation, which is vital for occupant comfort and health.
Industrial Process Control
In manufacturing and chemical processing, maintaining precise pressure levels is critical for safety and product quality. DP sensors are used to monitor pressure differentials in pipelines, reactors, and storage tanks, helping operators maintain optimal conditions.
For example, in a chemical reactor, a DP sensor can help ensure that the pressure difference between the reactor and the surrounding environment remains within safe limits. This monitoring prevents potential leaks or catastrophic failures, safeguarding both personnel and equipment. Moreover, in industries like pharmaceuticals, where product consistency is paramount, DP sensors can assist in maintaining the delicate balance of pressure required for specific reactions, thereby enhancing the overall quality and efficacy of the final product.
Water and Wastewater Management
In water treatment facilities, DP sensors are vital for monitoring the pressure in filtration systems and ensuring effective treatment processes. By measuring the pressure difference across filters, operators can determine when maintenance is required, ensuring consistent water quality.
Furthermore, in wastewater management, DP sensors help monitor the pressure in various stages of treatment, allowing for efficient operation and compliance with environmental regulations. These sensors also facilitate the optimization of pumping systems by providing real-time data on pressure changes, enabling operators to adjust flow rates as necessary. This not only improves the efficiency of the treatment process but also contributes to sustainable water management practices, reducing energy consumption and operational costs.
Benefits of Using DP Sensors
The integration of differential pressure sensors into industrial processes offers numerous benefits. These advantages contribute to increased efficiency, safety, and overall operational excellence.
Enhanced Process Efficiency
One of the primary benefits of DP sensors is their ability to enhance process efficiency. By providing real-time data on pressure differentials, operators can make informed decisions to optimize system performance. This capability leads to reduced energy consumption, lower operational costs, and improved product quality.
For instance, in an HVAC system, monitoring the pressure drop across filters allows for timely maintenance, ensuring that the system operates at peak efficiency. Similarly, in industrial processes, maintaining optimal pressure differentials can prevent product spoilage and reduce waste. Additionally, the data collected by DP sensors can be analyzed over time to identify trends, enabling predictive maintenance strategies that further enhance operational efficiency. This proactive approach not only minimizes unplanned downtime but also extends the lifespan of equipment by ensuring that it operates within its optimal parameters.
Improved Safety
Safety is paramount in any industrial setting, and DP sensors play a crucial role in ensuring safe operations. By continuously monitoring pressure differentials, these sensors help detect anomalies that could indicate potential hazards.
For example, in a chemical processing plant, a sudden change in pressure differential could signal a leak or equipment failure. Early detection through DP sensors allows for prompt intervention, reducing the risk of accidents and protecting both personnel and the environment. Furthermore, the incorporation of advanced analytics and alarm systems with DP sensors can provide operators with immediate alerts, allowing for swift action in critical situations. This not only fosters a culture of safety within the workplace but also ensures compliance with regulatory standards, which can be vital for maintaining operational licenses and avoiding legal repercussions.
Cost Savings
Investing in differential pressure sensors can lead to significant cost savings over time. By optimizing processes and enhancing safety, organizations can reduce maintenance costs, prevent downtime, and avoid costly accidents.
Moreover, the ability to monitor and control processes more effectively can lead to lower energy consumption and waste, translating into further savings. Ultimately, the return on investment for DP sensors can be substantial, making them a wise choice for many industries. In addition to direct cost savings, companies may also experience indirect benefits such as improved customer satisfaction due to higher product quality and reliability. This can lead to increased market share and profitability, as customers are more likely to remain loyal to brands that consistently deliver superior products and services. The long-term financial health of an organization can be significantly bolstered by the strategic implementation of DP sensors, making them an essential component of modern industrial operations.
Choosing the Right DP Sensor
Selecting the appropriate differential pressure sensor for a specific application requires careful consideration of several factors. Understanding these factors can help ensure optimal performance and reliability.
Measurement Range
The measurement range of a DP sensor is one of the most critical factors to consider. It is essential to choose a sensor that can accurately measure the expected pressure differentials in the application. Sensors with too narrow a range may lead to inaccurate readings, while those with an excessively wide range may lack the sensitivity needed for precise measurements. Additionally, it is important to consider the dynamic range of the sensor, which refers to the range over which the sensor can accurately respond to changes in pressure. A sensor with a wide dynamic range can adapt to fluctuating conditions, making it suitable for applications where pressure differentials can vary significantly over time.
Accuracy and Precision
Accuracy and precision are vital characteristics of any measurement device, and DP sensors are no exception. When selecting a sensor, it is important to consider the required accuracy for the specific application. High-accuracy sensors may be necessary for critical processes, while less stringent applications may allow for lower precision. Furthermore, it is essential to understand the difference between accuracy and precision; accuracy refers to how close a measurement is to the true value, while precision indicates the consistency of repeated measurements. Therefore, selecting a sensor with both high accuracy and precision is crucial for applications that demand reliable data, such as in pharmaceutical manufacturing or aerospace testing.
Environmental Considerations
The operating environment can significantly impact the performance of DP sensors. Factors such as temperature, humidity, and the presence of corrosive substances should be taken into account when selecting a sensor. Choosing a sensor designed to withstand specific environmental conditions ensures reliable operation and longevity. For instance, sensors used in outdoor applications may require additional protection against UV radiation and moisture, while those in industrial settings may need to resist dust and chemical exposure. Additionally, understanding the potential for vibration and shock in the application can guide the selection of a sensor with appropriate mechanical durability, ensuring that it can maintain accuracy even in challenging conditions.
Future Trends in DP Sensor Technology
The field of differential pressure sensing is continuously evolving, driven by advancements in technology and the growing demand for more efficient and reliable measurement solutions. Several trends are shaping the future of DP sensors.
Integration with IoT
The Internet of Things (IoT) is revolutionizing the way industries operate, and DP sensors are no exception. The integration of IoT technology allows for real-time data collection and analysis, enabling operators to monitor processes remotely and make data-driven decisions.
With IoT-enabled DP sensors, organizations can achieve greater visibility into their operations, leading to improved efficiency and reduced downtime. This connectivity also facilitates predictive maintenance, allowing for timely interventions before issues escalate. Furthermore, the data collected can be analyzed using advanced algorithms and machine learning techniques, providing insights that were previously unattainable. This not only enhances operational efficiency but also fosters a culture of continuous improvement within organizations.
Advancements in Sensor Technology
As technology continues to advance, DP sensors are becoming more sophisticated. Innovations in materials, design, and manufacturing processes are leading to sensors that are more accurate, reliable, and durable.
For instance, the development of MEMS (Micro-Electro-Mechanical Systems) technology is enabling the production of smaller, more sensitive sensors that can be used in a wider range of applications. These advancements are driving down costs and expanding the possibilities for differential pressure measurement. Additionally, the incorporation of smart materials and nanotechnology is paving the way for sensors that can operate under extreme conditions, such as high temperatures and corrosive environments, thus broadening their applicability in industries like aerospace and chemical processing.
Increased Focus on Sustainability
As industries strive to become more sustainable, the role of DP sensors in promoting energy efficiency and waste reduction is becoming increasingly important. Sensors that provide accurate measurements can help organizations optimize their processes, leading to reduced energy consumption and lower environmental impact.
Moreover, as regulations around sustainability become more stringent, the demand for reliable measurement solutions will continue to grow. DP sensors will play a pivotal role in helping organizations meet these challenges. In addition to monitoring energy use, these sensors can also assist in tracking emissions and ensuring compliance with environmental standards. This dual functionality not only enhances operational transparency but also positions companies as responsible stewards of the environment, which can be a significant competitive advantage in today’s eco-conscious market.
Conclusion
In summary, differential pressure sensors are essential devices that provide critical insights into various industrial processes. Their ability to measure pressure differentials accurately contributes to enhanced efficiency, improved safety, and significant cost savings.
As technology continues to evolve, the future of DP sensors looks promising, with advancements in IoT integration, sensor technology, and a growing focus on sustainability. Organizations that invest in high-quality DP sensors will be better positioned to optimize their operations and meet the challenges of an ever-changing industrial landscape.
Understanding the functionality, applications, and benefits of DP sensors is crucial for making informed decisions in process control and automation. By leveraging these powerful tools, industries can achieve operational excellence and drive continuous improvement.