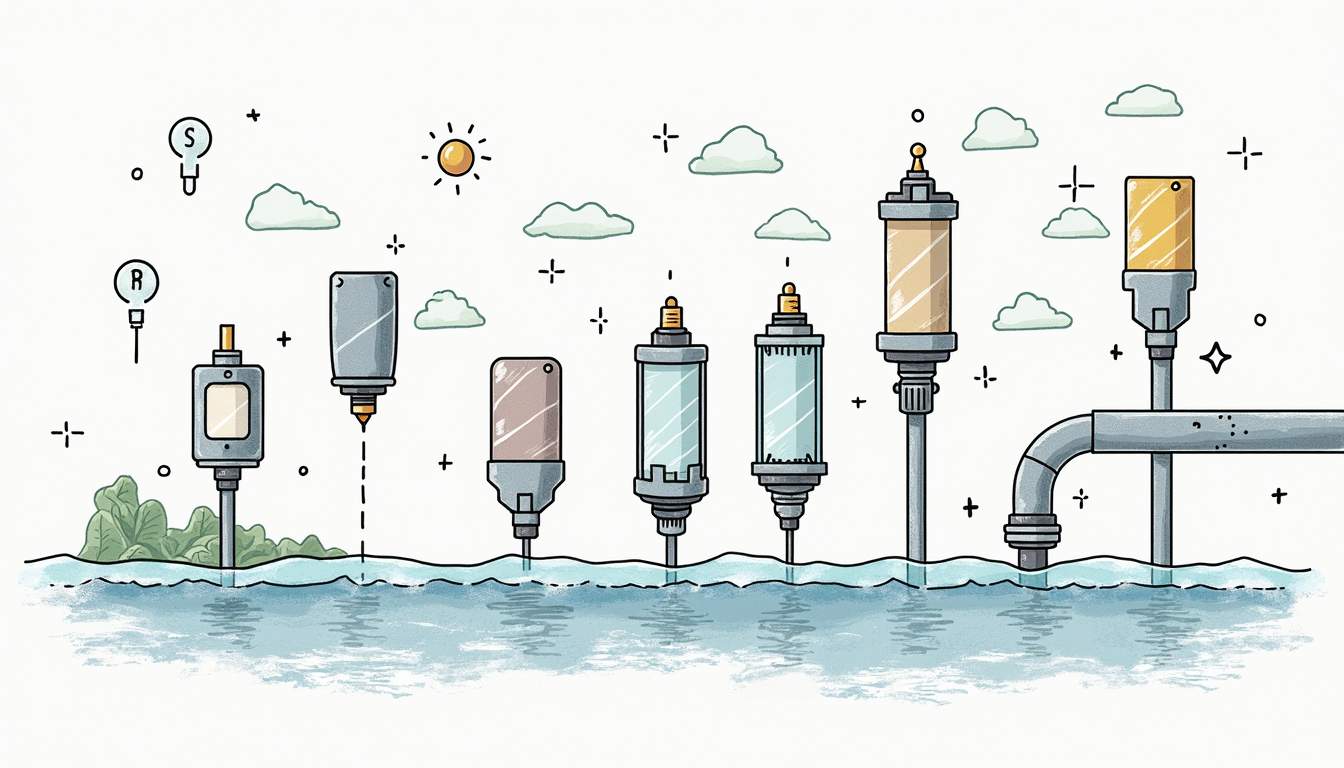
Understanding Float Sensors: Types, Applications, and Benefits
Float sensors play a critical role in various industries by providing reliable and accurate measurements of liquid levels. These sensors are essential for ensuring the safe and efficient operation of systems that rely on liquid management, such as water treatment facilities, oil and gas industries, and even household appliances. This article delves into the different types of float sensors, their applications, and the benefits they offer.
What Are Float Sensors?
Float sensors are devices designed to detect the level of liquid within a tank or container. They operate on the principle of buoyancy, where a float rises and falls with the liquid level, triggering a switch or sending a signal to a monitoring system. These sensors are crucial for maintaining optimal liquid levels, preventing overflow, and ensuring that systems function smoothly. Float sensors are widely used in various industries, including water treatment, HVAC systems, and even automotive applications, highlighting their versatility and importance in modern technology.
How Float Sensors Work
The basic operation of a float sensor involves a buoyant object, typically referred to as a float, which moves up and down with the changing liquid level. As the float moves, it activates a switch or sends an electrical signal to a control system. This mechanism can be mechanical, magnetic, or electronic, depending on the design of the float sensor. The choice of technology often depends on the specific application requirements, such as the type of liquid being measured, the required accuracy, and environmental conditions.
In mechanical float sensors, the float is connected to a lever that opens or closes a switch at predetermined liquid levels. These sensors are straightforward and cost-effective, making them popular for basic applications. Magnetic float sensors use a magnet within the float to activate reed switches or Hall effect sensors, providing a non-contact method of level detection. This non-contact feature not only enhances reliability but also minimizes maintenance needs, as there are fewer moving parts subject to wear. Electronic float sensors often utilize capacitive or ultrasonic technology for more precise measurements, enabling them to function effectively in more complex systems where accuracy is paramount.
Types of Float Sensors
Float sensors come in various types, each suited for specific applications and environments. Understanding the different types can help in selecting the right sensor for a particular need. The choice of float sensor can significantly impact the efficiency and safety of the system it is integrated into, making it essential to consider the operational context.
Mechanical Float Switches
Mechanical float switches are the simplest form of float sensors. They consist of a float attached to a lever that operates a switch. When the liquid level rises or falls, the float moves, causing the lever to activate or deactivate the switch. These sensors are commonly used in sump pumps and water tanks, where they help manage water levels effectively. Their straightforward design allows for easy installation and maintenance, making them an ideal choice for residential and commercial applications alike.
Magnetic Float Sensors
Magnetic float sensors utilize a float containing a magnet that interacts with reed switches or Hall effect sensors located outside the tank. This design allows for non-contact level detection, reducing wear and tear on the components. They are widely used in applications where reliability and longevity are crucial, such as in fuel tanks and industrial liquid storage. The ability to operate without direct contact with the liquid also makes them suitable for use in environments where contamination is a concern, ensuring that the integrity of the liquid remains intact.
Capacitive Float Sensors
Capacitive float sensors measure the change in capacitance caused by the presence of liquid. These sensors can detect liquid levels without direct contact, making them ideal for corrosive or hazardous liquids. They are often employed in chemical processing and food and beverage industries, where maintaining strict safety and hygiene standards is essential. Capacitive sensors can also be finely tuned to detect small changes in liquid levels, providing a level of precision that is beneficial in applications where exact measurements are critical. Their adaptability to various liquid types further enhances their utility across diverse sectors.
Applications of Float Sensors
Float sensors find applications across various industries, demonstrating their versatility and importance in liquid level management. Here are some key areas where float sensors are commonly used:
Water and Wastewater Management
In water treatment plants and wastewater facilities, float sensors are essential for monitoring liquid levels in tanks and basins. They help prevent overflow, ensure proper functioning of pumps, and maintain optimal water levels for treatment processes. By providing real-time data, float sensors contribute to efficient water management and environmental protection. Moreover, the integration of float sensors with automated control systems allows for remote monitoring and management, enabling operators to respond quickly to any irregularities. This capability is particularly crucial in urban areas where the risk of flooding can have severe consequences, making float sensors a vital component in safeguarding communities.
Oil and Gas Industry
The oil and gas industry relies heavily on float sensors for monitoring liquid levels in storage tanks and pipelines. These sensors help prevent spills and ensure safe operations by providing accurate level readings. Additionally, they are used in well monitoring systems to manage the extraction process effectively. The precision offered by float sensors is critical, as even minor inaccuracies can lead to significant financial losses or environmental hazards. Furthermore, advancements in float sensor technology, such as wireless communication and enhanced durability, have made them even more valuable in harsh environments, where traditional monitoring methods may fail. This innovation not only improves safety but also optimizes resource management in a sector that is constantly under scrutiny for its environmental impact.
Household Appliances
Float sensors are commonly found in household appliances such as washing machines and dishwashers. They help regulate water levels, ensuring that the appliances operate efficiently and safely. By detecting when to fill or drain water, float sensors enhance the functionality and longevity of these devices. In addition to traditional applications, newer models of household appliances are increasingly incorporating smart technology, allowing float sensors to communicate with home automation systems. This integration enables users to monitor and control their appliances remotely, providing convenience and energy savings. As consumers become more environmentally conscious, the role of float sensors in promoting water efficiency and reducing waste is becoming more significant, making them an essential feature in modern home design.
Benefits of Using Float Sensors
Incorporating float sensors into liquid management systems offers numerous benefits, making them a preferred choice for many industries. Here are some of the key advantages:
Accuracy and Reliability
Float sensors provide highly accurate liquid level measurements, which are crucial for maintaining optimal operational conditions. Their reliability ensures that systems function smoothly without unexpected interruptions. This accuracy is particularly important in industries where precise liquid levels are critical for safety and efficiency. For instance, in the food and beverage industry, maintaining specific liquid levels can prevent contamination and ensure product quality. Similarly, in chemical processing, even slight deviations in liquid levels can lead to hazardous situations, making float sensors an essential component for safety protocols.
Cost-Effectiveness
Float sensors are generally affordable and easy to install, making them a cost-effective solution for liquid level monitoring. Their durability and low maintenance requirements further enhance their value, as they reduce the need for frequent replacements or repairs. This cost-effectiveness is especially beneficial for small to medium-sized enterprises that may have limited budgets for equipment. Additionally, the long lifespan of float sensors means that businesses can allocate their resources more efficiently, investing in other critical areas of operation rather than frequent sensor replacements.
Versatility
With various types of float sensors available, they can be used in a wide range of applications and environments. Whether it’s in a simple water tank or a complex industrial system, there is a float sensor suitable for the task. This versatility makes them an invaluable tool across different sectors. For example, in wastewater treatment facilities, float sensors help monitor levels in settling tanks, ensuring proper treatment processes. In HVAC systems, they can regulate water levels in cooling towers, optimizing energy efficiency. Their adaptability to different liquids, including corrosive substances, further expands their application range, making them indispensable in industries such as pharmaceuticals and oil and gas.
Ease of Integration
Another significant advantage of float sensors is their ease of integration into existing systems. Many modern float sensors come equipped with standard interfaces that allow for seamless connectivity with various control systems, including PLCs (Programmable Logic Controllers) and SCADA (Supervisory Control and Data Acquisition) systems. This compatibility facilitates real-time monitoring and control, enabling operators to respond swiftly to any changes in liquid levels. Furthermore, the ability to integrate float sensors with alarms and notifications enhances operational safety, alerting personnel to potential issues before they escalate into serious problems.
Environmental Impact
Float sensors also contribute positively to environmental sustainability efforts. By ensuring that liquid levels are maintained within optimal ranges, they help prevent overflows and spills that could lead to environmental contamination. In industries such as agriculture, float sensors can optimize irrigation systems, conserving water and reducing waste. Their role in monitoring and managing liquid levels efficiently aligns with the growing emphasis on sustainable practices across various sectors, making them not only a practical choice but also a responsible one for businesses aiming to reduce their ecological footprint.
Choosing the Right Float Sensor
Selecting the appropriate float sensor for a specific application requires careful consideration of several factors. Understanding the requirements of the system is essential to ensure optimal performance.
Consider the Liquid Type
The type of liquid being monitored plays a significant role in determining the right float sensor. For instance, corrosive liquids may require non-contact sensors, while viscous liquids might necessitate a mechanical float switch. Assessing the chemical properties of the liquid is crucial for selecting a compatible sensor. Additionally, the presence of particulates or bubbles in the liquid can influence the choice; for example, a float sensor designed for clear liquids may not perform well in turbid or foamy conditions. Therefore, it is essential to conduct a thorough analysis of the liquid's characteristics, including pH levels, density, and potential for sedimentation, to ensure the chosen sensor will function reliably over time.
Environmental Conditions
Environmental factors such as temperature, pressure, and the presence of contaminants can affect the performance of float sensors. It’s important to choose sensors that can withstand the specific conditions of the application. For example, sensors used in high-temperature environments may need special materials to ensure durability. Moreover, factors like humidity and exposure to UV light can degrade sensor components, necessitating the selection of robust materials and protective coatings. In outdoor applications, for instance, sensors may require additional weatherproofing to prevent damage from rain or extreme temperatures. Understanding the full scope of environmental conditions will help in selecting a float sensor that not only meets operational requirements but also has a long service life.
Required Accuracy and Range
The required accuracy and measurement range are also critical considerations. Some applications may demand high precision, while others may function adequately with less accuracy. Understanding the specific needs of the application will guide the selection process. For example, in applications involving critical fluid levels—such as in medical devices or aerospace systems—high accuracy is paramount to prevent failures. Conversely, in less critical applications, a sensor with a broader range and lower precision might suffice. It is also worth noting that some advanced float sensors come equipped with digital outputs and integrated diagnostics, which can enhance measurement reliability and provide real-time data monitoring. This added functionality can be particularly beneficial in complex systems where maintaining optimal fluid levels is essential for operational efficiency.
Future Trends in Float Sensor Technology
The field of float sensors is continuously evolving, with advancements in technology leading to improved performance and new applications. Here are some trends shaping the future of float sensor technology:
Integration with IoT
As the Internet of Things (IoT) continues to expand, float sensors are increasingly being integrated into smart systems. This integration allows for real-time monitoring and data analysis, enhancing decision-making processes and operational efficiency. IoT-enabled float sensors can provide alerts and notifications, enabling proactive management of liquid levels. Furthermore, the data collected by these sensors can be analyzed to identify patterns and trends, leading to predictive maintenance and optimized resource allocation. For instance, industries such as water treatment and agriculture can significantly benefit from this technology, as it allows for precise control over water usage and quality, ultimately leading to more sustainable practices.
Advanced Materials and Designs
Innovations in materials and sensor designs are leading to more robust and reliable float sensors. New materials can enhance resistance to corrosive environments and extreme temperatures, while advanced designs improve sensitivity and accuracy. These developments are paving the way for float sensors to be used in more challenging applications. For example, sensors made from advanced polymers or coated with specialized materials can withstand harsh chemicals found in industrial settings, while also being lightweight and easy to install. Additionally, miniaturization of sensor components is enabling the creation of compact float sensors that can be deployed in tight spaces, making them suitable for a broader range of applications, from household appliances to large-scale industrial processes.
Increased Automation
Automation is becoming a key focus in many industries, and float sensors are no exception. The demand for automated liquid level management systems is driving the development of more sophisticated float sensors that can operate autonomously. This trend is expected to enhance efficiency and reduce human intervention in liquid management processes. With the integration of machine learning algorithms, these sensors can learn from historical data and adapt their responses based on changing conditions. For instance, in manufacturing environments, automated float sensors can adjust fluid levels in real-time, ensuring optimal operation of machinery and preventing costly downtimes. As industries strive for greater efficiency and lower operational costs, the role of automated float sensors will undoubtedly become more prominent, leading to smarter and more responsive liquid management systems.
Conclusion
Float sensors are indispensable tools for monitoring liquid levels across various industries. Their ability to provide accurate and reliable measurements makes them essential for maintaining operational efficiency and safety. With a range of types available, float sensors can be tailored to suit specific applications, ensuring optimal performance.
As technology continues to advance, the future of float sensors looks promising, with trends such as IoT integration and increased automation set to enhance their capabilities further. Understanding the different types, applications, and benefits of float sensors is crucial for making informed decisions in liquid level management.
Investing in the right float sensor technology can lead to significant improvements in operational efficiency, safety, and cost-effectiveness. As industries evolve, float sensors will undoubtedly remain a vital component in the effective management of liquid systems.