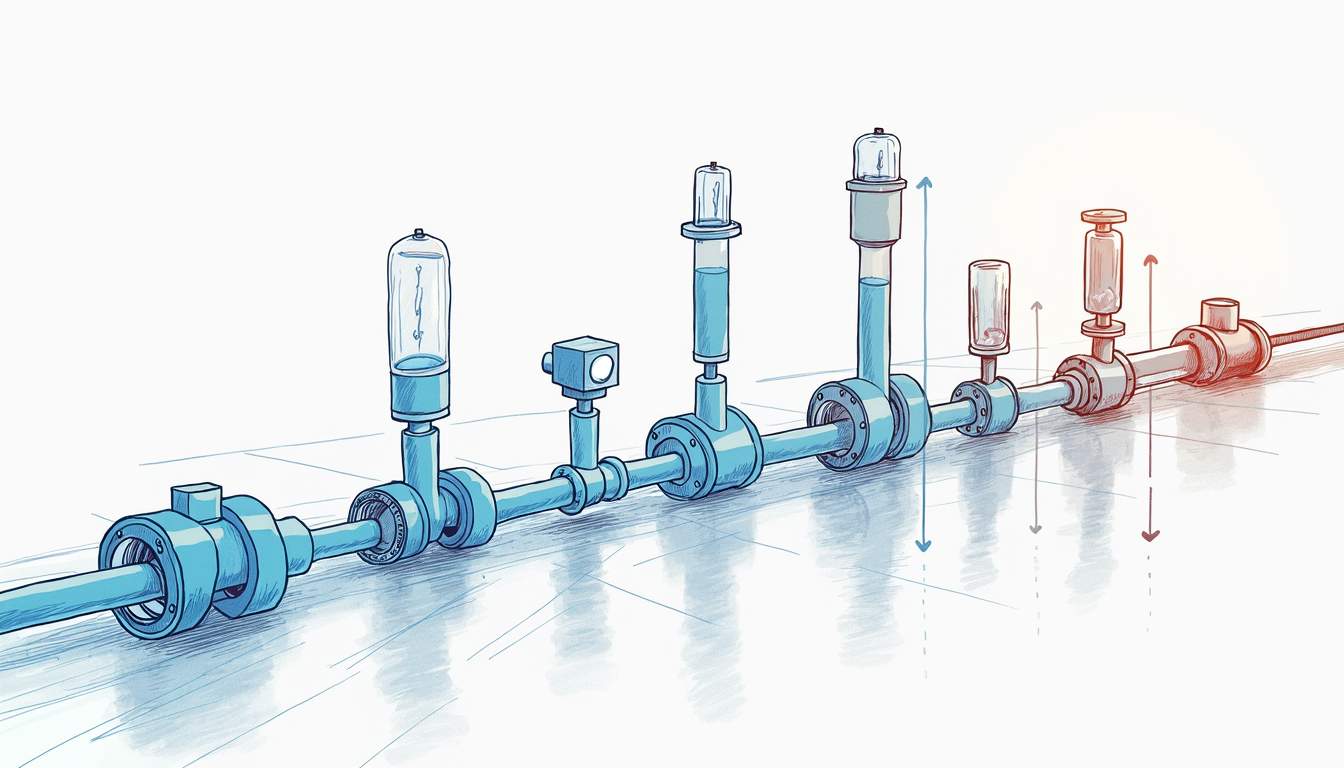
Understanding Flow Meter Sensors: Types, Applications, and Benefits
In the realm of industrial automation and process control, flow meter sensors play a pivotal role in measuring the flow rate of liquids and gases. These instruments are essential for a wide range of applications, from water treatment facilities to oil and gas industries. Understanding the various types of flow meter sensors, their applications, and the benefits they provide can significantly enhance operational efficiency and accuracy.
What is a Flow Meter Sensor?
A flow meter sensor is a device used to measure the flow rate of a fluid—be it a liquid or gas—through a pipe or conduit. These sensors can provide real-time data, which is crucial for monitoring and controlling processes in various industries. The data collected by flow meters can help in optimizing resource usage, ensuring safety, and maintaining regulatory compliance.
Flow meter sensors operate on different principles, and their choice often depends on the specific requirements of the application, including the type of fluid, flow conditions, and required accuracy. Understanding these principles is key to selecting the right flow meter for a given task.
There are several types of flow meter sensors, each designed to cater to specific applications. For instance, electromagnetic flow meters are particularly effective for measuring the flow of conductive liquids, making them ideal for water treatment facilities. On the other hand, ultrasonic flow meters utilize sound waves to determine the flow rate, which allows for non-invasive measurements, making them suitable for applications where maintaining the integrity of the fluid is crucial, such as in food and beverage processing. Additionally, thermal mass flow meters are often used in gas applications, providing accurate readings even at low flow rates, which is essential for industries like HVAC and natural gas distribution.
Moreover, advancements in technology have led to the development of smart flow meters that integrate with IoT systems, allowing for remote monitoring and data analysis. These smart devices can alert operators to anomalies in flow patterns, enabling proactive maintenance and reducing downtime. The ability to collect and analyze data over time also aids in predictive maintenance, ensuring that systems remain efficient and reducing the likelihood of costly failures. As industries continue to evolve, the role of flow meter sensors becomes increasingly vital, not only for operational efficiency but also for sustainability efforts, as they help in minimizing waste and optimizing resource consumption.
Types of Flow Meter Sensors
Flow meter sensors can be categorized based on their operating principles, construction, and application. Below are some of the most common types of flow meter sensors used in various industries.
1. Mechanical Flow Meters
Mechanical flow meters utilize moving parts to measure the flow of a fluid. These devices are often simple in design and can be very effective for specific applications. Common types include:
- Positive Displacement Meters: These meters measure the volume of fluid by trapping a fixed amount of liquid and then counting the number of times this volume passes through the meter. They are highly accurate and suitable for low flow rates.
- Rotary Vane Meters: These meters use a rotating vane to measure flow. The speed of rotation correlates with the flow rate, making them suitable for various applications, including water and oil measurement.
Mechanical flow meters are often favored in applications where simplicity and reliability are paramount. For instance, in the food and beverage industry, positive displacement meters are commonly used to ensure precise ingredient measurements, which is crucial for maintaining product quality. Additionally, the rugged design of rotary vane meters makes them particularly effective in harsh environments, where other types of meters might fail due to exposure to extreme conditions.
2. Electromagnetic Flow Meters
Electromagnetic flow meters operate on Faraday's law of electromagnetic induction. When a conductive fluid flows through a magnetic field, it generates a voltage proportional to the flow rate. These meters are ideal for measuring the flow of conductive liquids, such as water and slurries.
One of the main advantages of electromagnetic flow meters is their lack of moving parts, which minimizes wear and tear, leading to longer service life and lower maintenance costs. They are also highly accurate and can handle a wide range of flow rates. This makes them particularly valuable in industries such as wastewater treatment, where the ability to measure varying flow conditions is essential for effective process control. Furthermore, electromagnetic flow meters can be equipped with advanced features like data logging and remote monitoring, enhancing operational efficiency and providing real-time insights into system performance.
3. Ultrasonic Flow Meters
Ultrasonic flow meters use sound waves to measure the flow rate of liquids and gases. There are two primary types:
- Transit-Time Meters: These meters measure the time it takes for an ultrasonic pulse to travel upstream and downstream. The difference in travel time is used to calculate flow rate.
- Doppler Meters: These meters measure the frequency shift of ultrasonic waves reflected off particles in the fluid. They are particularly useful for measuring flow in dirty or aerated liquids.
Ultrasonic flow meters are non-invasive and can be installed without disrupting existing piping systems, making them a popular choice for retrofit applications. Their ability to measure flow without direct contact with the fluid not only reduces contamination risks but also extends the lifespan of the meter itself. Additionally, ultrasonic flow meters can be used in a variety of applications, from monitoring water distribution in municipal systems to measuring fuel flow in industrial processes. Their versatility is further enhanced by the ability to calibrate them for different fluid types, ensuring accurate measurements across a wide range of conditions.
Applications of Flow Meter Sensors
Flow meter sensors are versatile instruments used across various industries. Their ability to provide accurate flow measurements is crucial for optimizing processes, ensuring safety, and maintaining compliance with regulations. Here are some key applications:
1. Water and Wastewater Treatment
In water treatment facilities, flow meters are essential for monitoring the flow of water through different stages of purification. They help in managing the distribution of treated water and ensuring that wastewater is processed efficiently.
Flow meters also play a vital role in monitoring effluent discharge to comply with environmental regulations. Accurate flow measurement is crucial for reporting and ensuring that the facility operates within permitted limits. Furthermore, these sensors can assist in detecting leaks or irregularities in the system, allowing for timely maintenance and reducing the risk of contamination. By integrating flow meters with automated control systems, facilities can optimize chemical dosing and enhance operational efficiency, ultimately leading to improved water quality.
2. Oil and Gas Industry
The oil and gas sector relies heavily on flow meter sensors for various applications, including production monitoring, custody transfer, and pipeline management. Accurate flow measurement is critical for billing and regulatory compliance.
Different types of flow meters are used depending on the nature of the fluid being measured, whether it be crude oil, natural gas, or refined products. The ability to withstand high pressures and corrosive environments is often a key consideration in selecting flow meters for this industry. Additionally, advanced technologies such as ultrasonic and magnetic flow meters are gaining popularity due to their non-invasive measurement capabilities and reduced maintenance requirements. These innovations not only enhance measurement accuracy but also contribute to safer operations by minimizing the risk of leaks and spills, which can have devastating environmental impacts.
3. Food and Beverage Industry
In the food and beverage sector, maintaining product quality and safety is paramount. Flow meter sensors are used to monitor the flow of ingredients, ensuring that recipes are followed accurately.
Hygienic flow meters, designed to meet stringent sanitary standards, are essential for applications such as dairy processing, brewing, and bottling. These meters help maintain product integrity while ensuring compliance with health regulations. Moreover, the integration of flow meters with digital monitoring systems allows for real-time data collection and analysis, enabling manufacturers to track production efficiency and identify potential issues before they escalate. This not only enhances the safety of the food products but also supports the industry's commitment to sustainability by minimizing waste and optimizing resource use throughout the production process.
Benefits of Using Flow Meter Sensors
The adoption of flow meter sensors in various industries offers numerous benefits that can significantly impact operational efficiency and cost savings. Here are some key advantages:
1. Enhanced Accuracy and Reliability
One of the primary benefits of flow meter sensors is their ability to provide accurate and reliable measurements. This accuracy is crucial for process control, inventory management, and regulatory compliance. By ensuring precise flow measurements, organizations can minimize waste and optimize resource utilization.
Moreover, the integration of advanced technologies such as ultrasonic and electromagnetic flow meters has further increased the precision of these devices. These modern sensors can measure flow rates with minimal pressure loss and are less susceptible to variations in temperature and viscosity, which enhances their reliability across diverse applications. Industries ranging from water treatment to food and beverage manufacturing have reported significant improvements in their operational metrics due to the adoption of these high-precision instruments.
2. Improved Process Efficiency
Flow meter sensors enable real-time monitoring of fluid flow, allowing for immediate adjustments to be made in response to changing conditions. This capability enhances process efficiency, reduces downtime, and improves overall productivity.
Additionally, the data collected from flow meters can be analyzed to identify trends and inefficiencies, leading to further improvements in operational processes. For instance, predictive analytics can be employed to forecast maintenance needs, thereby preventing unexpected equipment failures. This proactive approach not only ensures continuous operation but also extends the lifespan of the equipment, resulting in fewer interruptions and a smoother workflow. The ability to monitor multiple parameters simultaneously, such as flow rate, pressure, and temperature, allows operators to gain a comprehensive understanding of their processes, leading to smarter decision-making.
3. Cost Savings
Investing in flow meter sensors can lead to significant cost savings over time. Accurate flow measurements help prevent over-pumping, reduce energy consumption, and minimize product losses. Furthermore, the longevity and low maintenance requirements of many modern flow meters contribute to reduced operational costs.
In addition to direct savings, the implementation of flow meter sensors can also enhance compliance with environmental regulations, which can be costly if not adhered to. By accurately measuring and reporting fluid usage and emissions, companies can avoid hefty fines and improve their sustainability profile. Furthermore, the ability to monitor and control processes more effectively can lead to better resource allocation, ensuring that materials and energy are used efficiently, ultimately contributing to a healthier bottom line. As industries increasingly focus on sustainability and operational excellence, the role of flow meter sensors becomes even more critical in driving both economic and environmental benefits.
Choosing the Right Flow Meter Sensor
Selecting the appropriate flow meter sensor for a specific application requires careful consideration of several factors. Understanding these factors can help ensure the best performance and reliability.
1. Fluid Characteristics
The type of fluid being measured is one of the most critical factors in choosing a flow meter. Considerations include:
- Viscosity: Highly viscous fluids may require different flow meter technologies compared to low-viscosity fluids.
- Temperature and Pressure: Ensure that the flow meter can withstand the operating conditions.
- Conductivity: For electromagnetic flow meters, the fluid must be conductive.
Additionally, the presence of particulates or bubbles in the fluid can significantly affect measurement accuracy. For example, slurries or fluids with suspended solids may necessitate the use of specialized flow meters designed to handle such conditions without clogging or producing erroneous readings. Furthermore, chemical compatibility is crucial; the materials used in the flow meter must be resistant to corrosion or degradation when in contact with the fluid, ensuring longevity and reliability in the measurement process.
2. Flow Rate Range
Different flow meter sensors have varying flow rate capabilities. It is essential to select a meter that can accurately measure the expected flow rates in the application. Oversized or undersized meters can lead to inaccuracies and operational challenges.
Moreover, understanding the dynamic range of the flow meter is vital. Some applications may experience fluctuations in flow rates, and a meter with a wide turndown ratio can accommodate these variations without sacrificing accuracy. This adaptability is especially important in industries such as water treatment or chemical processing, where flow rates can change rapidly due to varying operational demands or system adjustments.
3. Installation and Maintenance Requirements
Consider the installation requirements of the flow meter sensor. Some meters may require specific mounting configurations or additional components. Maintenance needs should also be evaluated, as some flow meters are more complex and require regular servicing.
In addition to installation logistics, the ease of access for maintenance is a critical factor to consider. Flow meters that are difficult to reach can lead to increased downtime and higher maintenance costs. Some modern flow meters come equipped with self-diagnostic features, allowing for real-time monitoring of performance and alerts for maintenance needs, which can streamline operations and reduce the risk of unexpected failures. Furthermore, understanding the calibration requirements of the flow meter is essential, as regular calibration ensures that the measurements remain accurate over time, especially in applications where precision is paramount.
Future Trends in Flow Meter Technology
The flow meter industry is continually evolving, driven by advancements in technology and the increasing demand for accurate and reliable measurements. Here are some trends shaping the future of flow meter sensors:
1. Smart Flow Meters
With the rise of the Internet of Things (IoT), smart flow meters equipped with connectivity features are becoming increasingly popular. These meters can transmit real-time data to cloud-based platforms, enabling remote monitoring and data analysis.
Smart flow meters enhance operational efficiency by allowing for predictive maintenance, reducing downtime, and providing insights into process performance. Furthermore, these devices often come with built-in diagnostic capabilities, which can alert operators to potential issues before they escalate into costly failures. The integration of machine learning algorithms also allows these meters to adapt to changing conditions, ensuring that they maintain accuracy and reliability over time.
2. Integration with Automation Systems
As industries move towards greater automation, flow meter sensors are being integrated into broader control systems. This integration allows for seamless data exchange and coordinated control of various processes, leading to enhanced efficiency and reduced human intervention.
3. Advanced Data Analytics
The ability to collect and analyze large volumes of data from flow meter sensors is transforming how organizations operate. Advanced analytics tools can identify patterns, predict trends, and optimize processes, leading to improved decision-making and operational performance.
Conclusion
Flow meter sensors are indispensable tools in modern industrial applications, providing critical data that drives efficiency, safety, and compliance. Understanding the various types of flow meters, their applications, and the benefits they offer is essential for organizations looking to optimize their operations.
As technology continues to advance, the future of flow meter sensors promises even greater accuracy, connectivity, and integration with automation systems. By staying informed about these developments, businesses can leverage flow meter technology to enhance their processes and achieve significant cost savings.
In an ever-evolving industrial landscape, investing in the right flow meter sensor is not just a choice; it's a necessity for maintaining competitiveness and operational excellence.