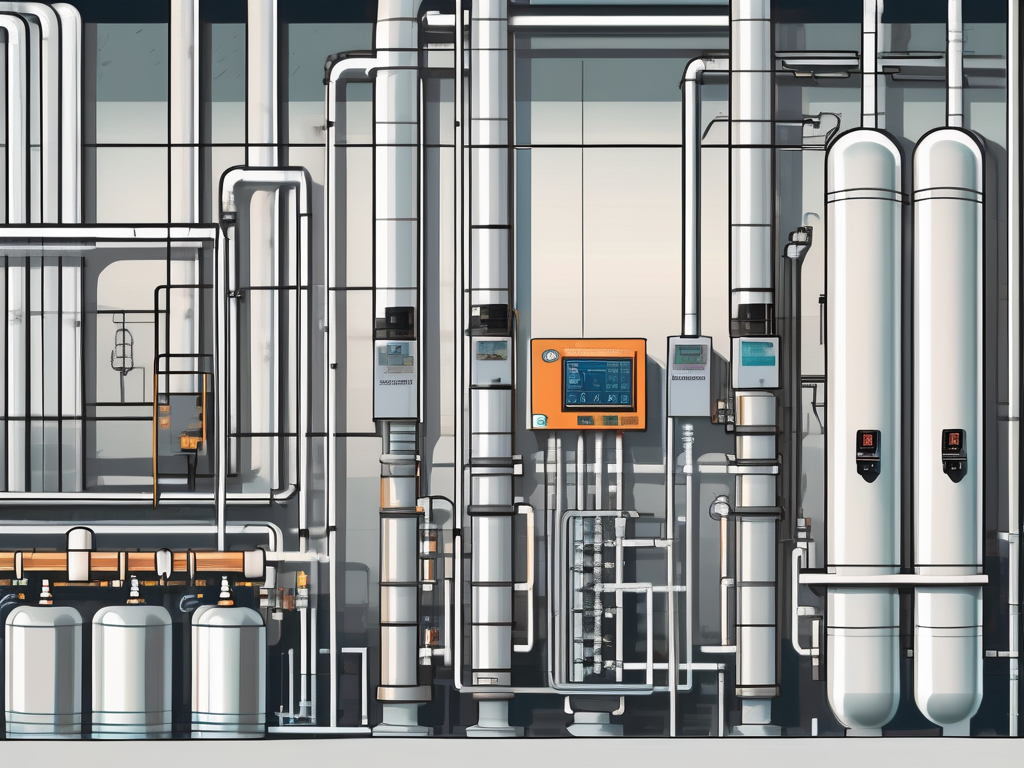
Understanding Lift Station Alarms: A Comprehensive Guide
Lift stations play a crucial role in the effective management of wastewater and stormwater systems. To ensure their optimal functioning, implementing a reliable alarm system is essential. This guide delves into each component of lift station alarms, highlighting their importance, types, maintenance, and future trends in the industry.
The Importance of Lift Station Alarms
Lift station alarms serve as the first line of defense for facilities that handle wastewater and stormwater. In the absence of these alarms, critical failures could fail to be detected until severe damage occurs.
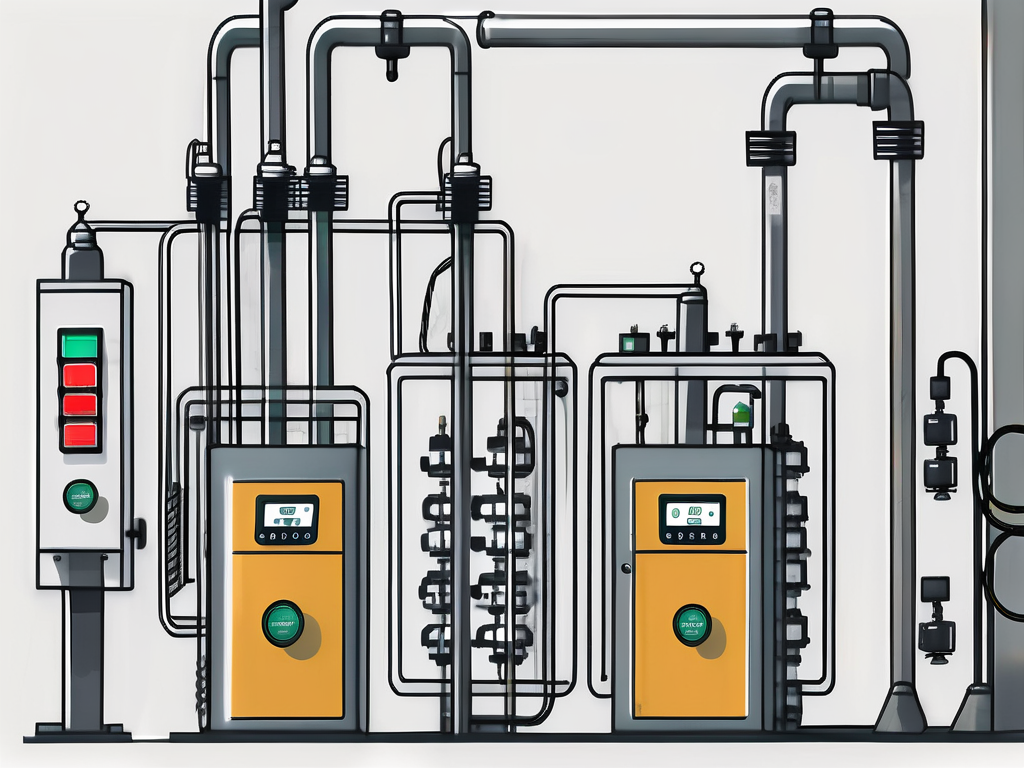
Role of Lift Station Alarms in Waste Management
By constantly monitoring the water levels, power supply, and operational status of pumps, lift station alarms help ensure that wastewater is transported efficiently and safely. These alarms alert operators to potential issues before they escalate into catastrophic events.
A properly functioning alarm system can prevent system overloads, reduce the risk of sewer overflows, and lower maintenance costs. This reliability is essential for both public health and environmental protection. Moreover, these systems are often integrated with advanced telemetry, allowing for data logging and trend analysis. This capability helps operators identify patterns over time, leading to proactive maintenance strategies that can extend the lifespan of equipment and improve overall system performance.
Safety Implications of Lift Station Alarms
Safety is paramount in wastewater management. Lift station alarms not only indicate equipment malfunctions or unusual conditions, but they also play a critical role in safeguarding human life. Should a power failure occur or a pump malfunction, the alarm system allows immediate action, thereby reducing injury risks to personnel.
Alarm systems also facilitate remote monitoring, a significant advantage for incident response. This real-time data collection provides operators with insights to act promptly and mitigate risks effectively. Furthermore, the integration of modern technology such as IoT devices enhances the capabilities of alarm systems, allowing for predictive analytics that can foresee potential failures before they happen. This proactive approach not only improves safety but also optimizes operational efficiency by minimizing downtime and ensuring that resources are allocated effectively during emergencies.
Different Types of Lift Station Alarms
Understanding the various types of lift station alarms is essential for selecting the appropriate system for your facility. Each type caters to specific conditions and operational needs.
High Water Alarms
High water alarms are activated when water levels exceed predetermined limits, signaling potential flooding or backup situations. These alarms are vital pathways for reducing the risk of wastewater spillage.
With sensor technology, high water alarms can notify operators not only through auditory signals but also via text or app notifications for immediate response, therefore enhancing operational efficiency. Furthermore, many modern systems can integrate with SCADA (Supervisory Control and Data Acquisition) systems, allowing for real-time monitoring and data logging. This integration enables operators to analyze trends over time, helping to predict potential issues before they escalate into serious problems.
Power Failure Alarms
Given that lift stations are primarily powered by electricity, power failure alarms are critical. These alarms alert operators when power is lost, ensuring emergency procedures can be implemented swiftly. This may involve starting backup generators or initiating alternative pumping protocols.
Power failure alarms help prevent operational downtime, which is crucial for maintaining wastewater management processes during unforeseen circumstances. In addition, many systems are now equipped with battery backup capabilities that allow for continued operation of alarms and critical monitoring systems, ensuring that operators remain informed even during extended outages. This feature not only enhances safety but also provides peace of mind to facility managers, knowing that their systems can withstand power interruptions.
Pump Failure Alarms
Pump failure alarms monitor the performance and operational status of pumps. They are designed to alert operators when a pump is not functioning correctly, allowing for quick troubleshooting and maintenance.
Early detection of pump failures not only prevents damage to the pump itself but also ensures continuous flow and reduces the risk of catastrophic system failure. Advanced pump failure alarms can also provide diagnostic information, such as vibration analysis and temperature readings, which help operators identify the root cause of the malfunction. This proactive approach to maintenance can significantly extend the lifespan of the equipment and minimize costly repairs, ultimately leading to a more reliable and efficient wastewater management system.
Components of a Lift Station Alarm System
To effectively monitor and control lift station operations, it is essential to understand the key components that make up an alarm system. Each component plays a specific role in ensuring timely alerts and safe operations.
Alarm Panel
The alarm panel serves as the central hub for monitoring all alarms and system notifications. This interface facilitates real-time communication between various components of the alarm system and the operators.
Modern alarm panels can include features such as touchscreen controls, logged data analytics, and remote access capabilities, which significantly enhance user experience and efficiency. Additionally, many advanced panels are equipped with customizable alert settings, allowing operators to prioritize notifications based on urgency. This flexibility ensures that critical issues are addressed promptly while minimizing unnecessary distractions from less significant alerts.
Float Switches
Float switches are mechanical devices that monitor the liquid level within the lift station. They trigger alarms when the water rises to a certain level, serving as an essential component of high water alarm systems.
These switches are typically easy to install and maintain, making them a popular choice for wastewater management systems. Furthermore, float switches can be designed to operate in various environmental conditions, ensuring reliability in both standard and extreme scenarios. Some models even feature multiple floats, which can provide more granular monitoring of liquid levels, allowing for proactive management of potential overflow situations.
Backup Systems
Backup systems ensure that the alarm continues to function even in the event of a power outage. These systems may include battery backups or generators, offering peace of mind that critical notifications will still be sent out.
Investing in a robust backup system is crucial for ensuring uninterrupted service and compliance with safety regulations. In addition to traditional battery backups, some modern systems incorporate renewable energy sources, such as solar panels, to maintain functionality during extended outages. This not only enhances the reliability of the alarm system but also contributes to sustainability efforts by reducing reliance on conventional power sources. Moreover, regular maintenance and testing of these backup systems are vital to ensure they perform optimally when needed most, preventing any lapses in monitoring during critical times.
Troubleshooting Common Lift Station Alarm Issues
Even with a top-notch alarm system in place, operators may encounter certain issues. Understanding how to troubleshoot these problems can prevent extended downtime and service interruptions.
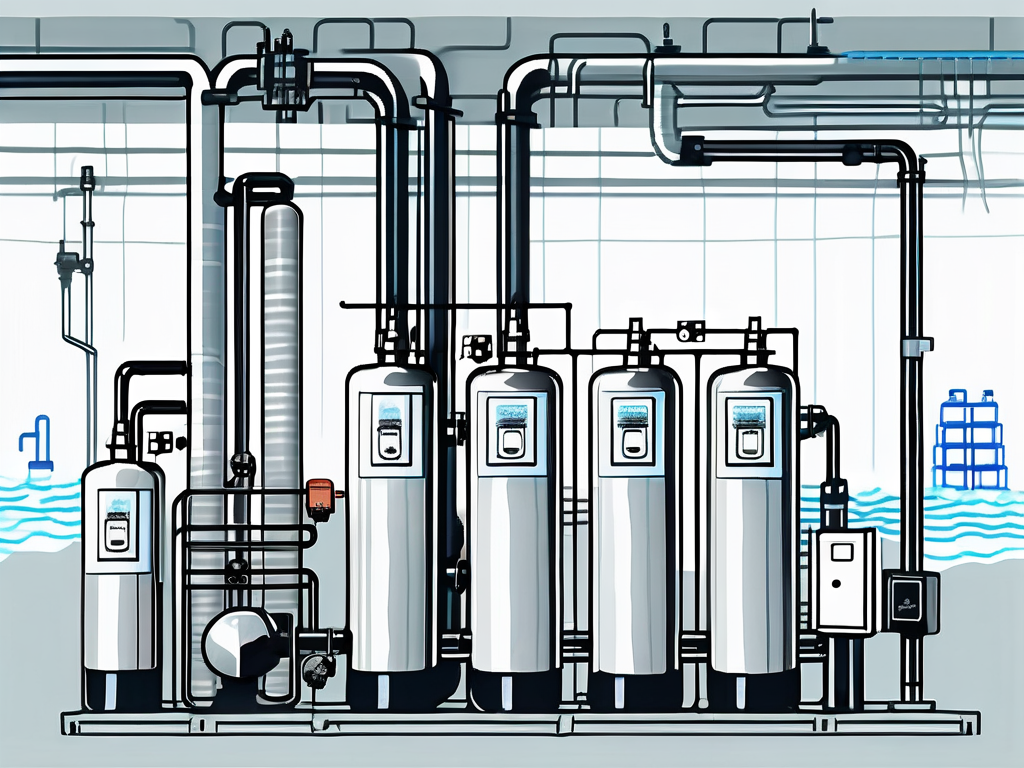
False Alarms
False alarms can be both frustrating and misleading for operators. Common causes may include faulty sensors, debris, or improper calibration. These false alerts not only lead to unnecessary panic but can also desensitize staff to alarms over time, potentially causing them to overlook genuine emergencies.
Regular inspection and maintenance are essential for minimizing these disturbances. Additionally, proper training can help operators respond appropriately and diagnose problems effectively. Implementing a routine checklist for sensor calibration and cleaning can significantly reduce the frequency of false alarms. Furthermore, utilizing advanced diagnostic tools can help pinpoint the exact cause of these issues, allowing for more efficient repairs and adjustments.
Alarm Won't Reset
When alarms fail to reset, it can indicate underlying issues such as malfunctioning components or the need for system reconfiguration. Troubleshooting procedures should involve checking the alarm settings and ensuring that sensors are functioning correctly. In some cases, the reset mechanism itself may be faulty, requiring a thorough examination of the control panel and its connections.
If problems persist, consulting the equipment's manual or contacting a qualified technician may be necessary for resolution. Keeping a log of alarm incidents can also be beneficial, as it allows operators to track patterns and identify recurring problems, which can lead to more effective long-term solutions.
Alarm Not Sounding
An alarm that does not emit sound can compromise safety measures and response time. Operators should first check the power supply and connections to ensure the alarm panel is operational. Additionally, verifying the volume settings and ensuring that the alarm is not in a silent mode can help troubleshoot the issue.
If the system is powered but the alarm still fails to activate, the alarm’s speaker or sound mechanism may require repairs or replacement. It’s also advisable to conduct regular sound tests to confirm that the alarm system is functioning as intended. In environments where noise levels are high, considering supplemental visual alarms, such as flashing lights, can enhance safety and ensure that alerts are noticed promptly, regardless of sound issues.
Maintenance and Inspection of Lift Station Alarms
Regular maintenance and inspections are vital for ensuring the reliability and accuracy of lift station alarm systems. Establishing a maintenance routine helps prevent unforeseen failures and prolongs the lifespan of the equipment. Given the critical role that lift stations play in wastewater management, neglecting these systems can lead to significant operational disruptions and environmental hazards.
Regular Inspection Schedule
Creating a regular inspection schedule can help maintain optimal functioning. Operators should review alarm settings, test each alarm type, and ensure all components are functioning correctly. It is beneficial to involve multiple team members in the inspection process to provide diverse insights and ensure that no detail is overlooked. This collaborative approach not only enhances the thoroughness of inspections but also fosters a culture of safety and accountability among staff.
Additionally, documenting these inspections allows for better tracking of performance over time and assists in identifying any persistent issues that may require further attention. Utilizing digital tools or maintenance management software can streamline this documentation process, making it easier to analyze trends and schedule future maintenance tasks efficiently.
Essential Maintenance Tasks
Routine maintenance tasks for lift station alarms may include cleaning sensors, checking connections, and replacing components as needed. Operators should also ensure that backup systems are regularly tested and operational. This includes verifying the functionality of battery backups and alternative power sources, which are crucial during power outages or system failures.
Staying on top of these tasks will minimize the risk of alarm failures, ultimately protecting both personnel and the integrity of the lift station. Furthermore, it is essential to provide ongoing training for operators to keep them informed about the latest technologies and best practices in alarm maintenance. Knowledgeable staff can better respond to alarms and take preventive measures, thereby enhancing the overall efficiency and safety of the lift station operations.
Choosing the Right Lift Station Alarm for Your Needs
Selecting the appropriate lift station alarm is critical for effective management and long-term functionality. Several factors should be considered during this process.
Factors to Consider
When choosing a lift station alarm, consider the environment in which it will operate, including potential exposure to moisture, temperature fluctuations, and the presence of corrosive substances. For example, if the lift station is located in a coastal area, the alarm system should be designed to withstand saltwater corrosion, which can significantly impact its longevity and reliability.
Additionally, think about the specific needs of your facility. For instance, a high-flow facility may prioritize high water alarms, while an aging facility may focus more on pump failure alarms due to increased risk in older equipment. It's also essential to assess the historical performance data of your lift station. Understanding past incidents can help you identify which alarms would have been most beneficial in preventing issues and can guide you in making a more informed decision.
Understanding Alarm Specifications
Familiarizing yourself with alarm specifications is crucial when evaluating different systems. Look for alarms that provide clear notification types, network connectivity for remote monitoring, and ease of installation and maintenance. Some modern systems even offer features like SMS or email alerts, enabling operators to respond quickly to any issues, regardless of their location.
Understanding specifications will ensure you select an alarm system that meets industry standards and aligns with your operational requirements. Additionally, consider the scalability of the alarm system. As your facility grows or changes, you may need to expand or modify your alarm capabilities. Choosing a system that allows for easy upgrades or integration with other monitoring technologies can save you time and resources in the long run. Furthermore, it's beneficial to evaluate the manufacturer's support and warranty options, as reliable customer service can be invaluable when troubleshooting or seeking replacements for faulty components.
The Future of Lift Station Alarms
The field of lift station alarms continues to evolve, influenced by technological advancements and the growing emphasis on environmental sustainability. Staying informed about these trends is vital for proactive management.
Technological Advancements
Innovations in the technology used within lift station alarms are redefining operational capabilities. Features such as IoT integration, artificial intelligence-driven monitoring, and cloud-based data analytics are becoming increasingly prevalent.
These advancements can streamline alarm management, improve data collection, and enhance overall decision-making processes, ultimately contributing to better performance and efficiency. For instance, IoT-enabled sensors can provide real-time data on the operational status of lift stations, allowing for immediate responses to potential issues before they escalate into significant problems. Additionally, machine learning algorithms can analyze historical data patterns to predict future failures, thereby enabling maintenance teams to perform preventative actions at optimal times.
Environmental Impact and Sustainability
With an increasing focus on sustainability, lift station alarms of the future will also be designed with eco-friendliness in mind. New systems will prioritize energy efficiency and utilize sustainable materials to lessen their environmental impact.
By investing in advanced, sustainable technologies, wastewater management facilities can not only comply with regulations but also contribute toward a healthier ecosystem. Moreover, the integration of renewable energy sources, such as solar panels, into lift station operations can further reduce carbon footprints. These eco-conscious designs not only benefit the environment but can also lead to cost savings in energy consumption over time, making them a wise investment for municipalities and private operators alike.
As the industry moves forward, collaboration among engineers, environmentalists, and technology developers will be crucial in shaping the future of lift station alarms. Engaging in cross-disciplinary partnerships can foster innovative solutions that address both operational efficiency and ecological responsibility, ensuring that lift stations are not only effective in their primary functions but also aligned with global sustainability goals.