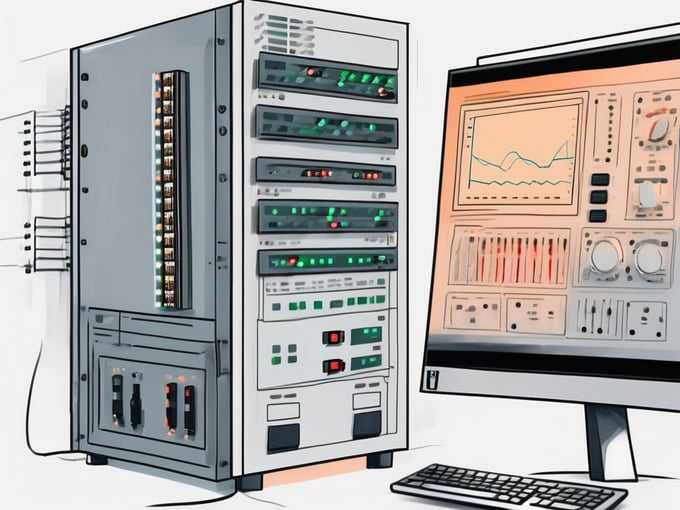
The Difference Between Remote Terminal Units (RTU) and Programmable Logic Controllers (PLC)
In the world of industrial automation, two key players stand out: Remote Terminal Units (RTUs) and Programmable Logic Controllers (PLCs). These devices are crucial in monitoring and controlling various processes, but understanding their differences is important in order to choose the right solution for your specific needs.
Understanding Remote Terminal Units (RTU)
Remote Terminal Units, commonly known as RTUs, are electronic devices used to monitor and control industrial processes remotely. They play a crucial role in various industries, ensuring efficient and reliable operation of critical systems. RTUs are often deployed in remote locations, where human intervention may be limited or impractical. These devices are specifically designed to withstand rugged environments, including extreme temperatures, humidity, and vibrations.
RTUs are equipped with inputs and outputs (I/O) that allow them to sense and control various parameters such as temperature, pressure, and flow. These data points are then communicated to a central control system, enabling real-time monitoring and decision-making. The ability of RTUs to collect and transmit data from multiple sensors and devices is a key advantage, as it provides a comprehensive overview of the industrial processes.
Key Features of RTUs:
- Highly reliable and robust design: RTUs are built to withstand harsh conditions and ensure uninterrupted operation. They are often equipped with redundant power supplies and communication modules to enhance reliability.
- Wide operating temperature range: RTUs can operate in extreme temperatures, ranging from scorching heat to freezing cold, making them suitable for a wide range of environments.
- Flexible communication capabilities: RTUs support various communication protocols, including Ethernet, serial, and wireless, allowing seamless integration with existing industrial networks.
- Exceptional data acquisition capabilities: RTUs can acquire data from a multitude of sensors and devices, including analog and digital inputs, enabling comprehensive monitoring and control of industrial processes.
Common Uses of RTUs:
- Oil and gas pipeline monitoring: RTUs are extensively used in the oil and gas industry to monitor pipeline operations, ensuring the safe and efficient transportation of petroleum products. They can detect leaks, pressure fluctuations, and other anomalies, triggering immediate actions to prevent accidents.
- Water and wastewater treatment: RTUs play a vital role in water and wastewater treatment plants, monitoring and controlling various processes such as pumping, filtration, and disinfection. They help maintain optimal water quality, prevent equipment failures, and ensure compliance with environmental regulations.
- Power distribution systems: RTUs are deployed in power distribution systems to monitor and control substations, transformers, and other critical components. They enable real-time monitoring of power consumption, voltage levels, and fault detection, facilitating efficient power distribution and minimizing downtime.
Unpacking Programmable Logic Controllers (PLC)
Programmable Logic Controllers, or PLCs, are another type of industrial control system. They are versatile devices that provide real-time control over various processes and machines. PLCs are designed to run automated sequences based on predetermined logic, allowing for precise control and automation of complex systems.
When it comes to the essential characteristics of PLCs, there are several key factors that make them stand out:
- Modular and scalable design: PLCs are built with a modular architecture, allowing for easy expansion and customization. This means that as the needs of a system change, additional modules can be added or removed without disrupting the overall functionality.
- Fast and accurate response times: PLCs are known for their ability to process and execute commands with incredible speed and precision. This is crucial in industrial settings where even the slightest delay or error can have significant consequences.
- Extensive memory for program storage: PLCs have ample memory capacity to store complex programs and instructions. This allows for the implementation of intricate control algorithms and logic, enabling the PLC to handle a wide range of tasks and scenarios.
- Support for various programming languages: PLCs are compatible with multiple programming languages, such as ladder logic, structured text, and function block diagrams. This flexibility allows programmers to choose the most suitable language for a specific application, making PLCs highly adaptable.
PLCs find applications in various industries and sectors. Some of the typical applications of PLCs include:
- Manufacturing assembly lines: PLCs play a crucial role in controlling and coordinating complex assembly line processes. They ensure that each step of the production process is executed accurately and efficiently, minimizing errors and maximizing productivity.
- Building automation systems: PLCs are widely used in building automation systems to control and monitor various functions, such as lighting, HVAC (heating, ventilation, and air conditioning), security systems, and access control. They provide centralized control and allow for the integration of different subsystems, enhancing energy efficiency and occupant comfort.
- Robotics and industrial machinery control: PLCs are the backbone of robotic systems and industrial machinery control. They enable precise and synchronized movement of robots, ensuring smooth operation and high precision in tasks such as material handling, welding, and assembly. PLCs also provide safety features, such as emergency stop functionality, to protect operators and equipment.
As technology continues to advance, PLCs are evolving to meet the ever-increasing demands of industrial automation. With their versatility, reliability, and extensive capabilities, PLCs are indispensable tools in modern industrial control systems.
Comparing RTU and PLC
While both RTUs (Remote Terminal Units) and PLCs (Programmable Logic Controllers) serve a similar purpose, there are distinct differences that set them apart. Let's explore these differences in more detail.
Similarities Between RTU and PLC
Both RTUs and PLCs offer remote monitoring and control capabilities. They provide real-time data acquisition, processing, and communication with the central control system. Additionally, both devices are programmable and can execute automated sequences based on predefined logic.
Distinct Differences Between RTU and PLC
One of the primary differences between RTUs and PLCs is their design and environmental suitability. RTUs are built to withstand harsh conditions like extreme temperatures, humidity, and vibration. They are designed for deployment in remote and uncontrolled environments.
For example, imagine an oil rig situated in the middle of the ocean. The RTUs installed on the rig are exposed to the corrosive saltwater mist, high winds, and constant movement caused by the waves. These rugged devices are designed to withstand such extreme conditions, ensuring reliable operation and continuous data acquisition.
On the other hand, PLCs are typically installed in controlled environments such as manufacturing plants or industrial facilities. These environments have stable temperatures, controlled humidity levels, and minimal exposure to external factors. PLCs in these settings focus on rapid response times and precise control, ensuring efficient and accurate operation of the machinery or processes they control.
Another crucial difference lies in the I/O (Input/Output) capabilities of RTUs and PLCs. RTUs are designed to handle a wide range of inputs and outputs, making them suitable for applications requiring extensive data acquisition.
Consider a large-scale solar power plant. The RTUs installed throughout the plant are responsible for monitoring and collecting data from various sensors, such as solar irradiance, temperature, and wind speed. These RTUs can handle numerous I/O points, allowing for comprehensive data acquisition and analysis. This data is then used to optimize the plant's performance and ensure maximum energy production.
On the other hand, PLCs often have a more modular design, allowing for scalability and customization of I/O modules based on specific application requirements. This flexibility is particularly useful in manufacturing processes where different machines or equipment may require varying I/O configurations.
For instance, in an automotive assembly line, PLCs are used to control and coordinate the movements of robots, conveyors, and other machinery. Each PLC can be equipped with different I/O modules, tailored to the specific needs of the machine it controls. This modular approach allows for efficient integration and synchronization of various components, ensuring smooth operation and high productivity.
In conclusion, while RTUs and PLCs share similarities in terms of remote monitoring and control capabilities, their design, environmental suitability, and I/O capabilities set them apart. The choice between an RTU and a PLC depends on the specific application requirements, environmental conditions, and the level of data acquisition and control needed.
Choosing Between RTU and PLC
When selecting between an RTU and PLC, several factors need to be considered to ensure the right choice for your application.
Both Remote Terminal Units (RTUs) and Programmable Logic Controllers (PLCs) are widely used in various industries for monitoring and controlling processes. While they serve similar purposes, there are important differences to consider when deciding which one is best suited for your specific needs.
Factors to Consider When Choosing RTU or PLC
- Application Requirements: Understand the specific needs of your application, including the required I/O points, environmental conditions, and communication protocols. This will help determine whether an RTU or PLC is better suited for your application.
- Scalability: Consider the future scalability requirements of your system. If your application demands potential expansion, a PLC with modular I/O capabilities may be a better fit. On the other hand, if your application requires remote monitoring and control in geographically dispersed locations, an RTU with its built-in communication capabilities may be more suitable.
- Programming and Configuration: Evaluate the programming and configuration options available for both RTUs and PLCs. PLCs typically offer a wide range of programming languages, such as ladder logic, function block diagrams, and structured text, making them more versatile for complex automation tasks. RTUs, on the other hand, often use proprietary programming languages that are specifically designed for remote monitoring and control applications.
- Reliability and Robustness: Consider the environmental conditions in which the RTU or PLC will be deployed. RTUs are known for their rugged design and ability to withstand harsh conditions, making them suitable for applications in industries such as oil and gas, where remote monitoring and control of pipelines is required. PLCs, on the other hand, are typically designed for use in controlled environments and may not be as robust as RTUs.
Industry-Specific Considerations for RTU and PLC Selection
Different industries have unique considerations when it comes to choosing between RTUs and PLCs. Here are a few examples:
- Oil and Gas Industry: RTUs are favored for remote monitoring and control of pipelines due to their rugged design and ability to handle extensive I/O. They can withstand extreme temperatures, humidity, and other harsh environmental conditions commonly found in oil and gas facilities.
- Manufacturing Plants: PLCs offer flexibility and rapid response times, making them ideal for complex automation tasks on assembly lines. They can handle high-speed processes and provide precise control over various manufacturing operations.
- Water and Wastewater Industry: The water and wastewater industry often relies on RTUs for monitoring critical parameters in remote treatment plants due to their robustness and communication capabilities. RTUs can collect data from sensors and transmit it to a central control system for analysis and decision-making.
By considering these factors and understanding the specific requirements of your application, you can make an informed decision between an RTU and PLC that best suits your needs.
The Future of RTU and PLC
As technology continues to advance, both RTUs and PLCs are evolving to meet the demand for more interconnected and intelligent industrial control systems.
With the rapid development of Internet of Things (IoT) and Industry 4.0, the future of RTUs (Remote Terminal Units) and PLCs (Programmable Logic Controllers) is promising. These two technologies are at the forefront of industrial automation, providing efficient and reliable control solutions for various industries.
Technological Advances in RTU and PLC
Advancements in RTU technology include increased connectivity options, such as cellular and satellite communication, enabling wider coverage and more efficient data transmission. This connectivity revolutionizes the way industrial systems are monitored and controlled. Real-time data can be collected from remote locations, allowing for faster decision-making and improved operational efficiency.
Moreover, RTUs are becoming smarter, incorporating advanced analytics and predictive maintenance capabilities to optimize system performance. These intelligent features enable proactive maintenance, reducing downtime and maximizing productivity. By analyzing historical data and detecting patterns, RTUs can predict potential failures and trigger preventive measures, saving time and resources.
On the other hand, PLCs are also undergoing transformative changes. The integration of machine learning algorithms and artificial intelligence is enabling predictive control and anomaly detection. By continuously learning from data patterns, PLCs can adapt and optimize control strategies to achieve better performance and energy efficiency.
Cloud connectivity is another trend that allows remote monitoring and increased collaboration across multiple sites. PLCs can securely transmit data to cloud platforms, enabling real-time monitoring and analysis. This cloud-based approach facilitates centralized control and provides valuable insights for decision-making and process optimization.
Predicted Trends for RTU and PLC Usage
In the future, the convergence of RTUs and PLCs is anticipated, blurring the lines between these technologies. This convergence is driven by the need for highly integrated and centralized control systems that combine the ruggedness of RTUs with the agility and intelligence of PLCs.
Furthermore, the rise of edge computing is expected to play a significant role in the future of RTUs and PLCs. Edge computing involves processing data closer to the source, reducing latency and enabling real-time control. This approach enhances the responsiveness and reliability of industrial control systems, especially in applications where immediate action is crucial.
As industries continue to embrace digital transformation, the demand for advanced control solutions will continue to grow. The future of RTUs and PLCs lies in their ability to adapt to changing requirements and integrate seamlessly with emerging technologies. The combination of connectivity, intelligence, and flexibility will shape the next generation of industrial control systems.
Ultimately, the choice between an RTU and PLC relies on the specific requirements of your application. Understanding the differences and assessing the needs of your industry will guide you in making the right decision for your control and automation needs.